What Is BMS in an Electric Vehicle (EV)?
- System that monitors and controls battery state and performance -
2023-10-20
A battery management system (BMS) monitors the state of a battery and eliminates variations in performance of individual battery cells to allow them to work uniformly. It is an important system that allows the battery to exert its maximum capability. The system is incorporated in an EV powered with a large-capacity lithium ion battery, and plays an important role in extending the service life of the battery and ensuring safe use of the battery. This article will discuss the functions and system configuration of the BMS, and will introduce electronic components making up the BMS as well.
What is a BMS?
Brief description of the BMS
A battery management system (BMS) monitors and controls the state of a battery, thereby allowing the battery to work safely for a long period. A battery (lithium ion battery) used in an EV deteriorates every time the battery discharges or is charged. These cycles of battery deterioration may lead to a drop in the vehicle performance. The BMS is an important solution to this problem. It monitors the state of the entire battery cells on a cell-by-cell basis and allows them to work uniformly by eliminating variations in individual batteries' performance.
What does the BMS do?
-
Monitoring : The BMS monitors the state of the entire battery cells on a cell-by-cell basis.
Voltage measurement:
The BMS measures the voltage of each battery cell or the overall voltage of the battery pack, thereby preventing an overcharging or excessive discharging.Current measurement:
The BMS measures the discharge current from the battery or the charge current to the battery. It checks the use status or the charged state of the battery and performs proper control.Temperature measurement:
The BMS constantly monitors the temperature of the battery through a temperature sensor. Using the battery within a proper temperature range ensures the safety of the battery and longer service life. -
Control:The BMS eliminates variations in performance of individual battery cells to allow them to work uniformly.
A large-capacity battery pack consists of a number of battery cells. These cells vary in performance, and deteriorate at different rates. For example, when a specific cell deteriorates faster than other cells do, it may affect the overall performance or service life of the battery pack. Such variations in performance or deterioration rate are eliminated by a function called "balancing."
Trends in the market and demand for the BMS
Today, the EV needs a motor with high power output and a large-capacity battery that allows for longer mileage and can be charged faster and efficiently. It is expected, for this reason, that more and more large-capacity batteries will be put on the market as in-EV batteries. It is also expected that a battery capable of supplying high-voltage power will be in demand. Electronic components making up the BMS are required to offer specific functions/performance for the future, which include "high power,” "highly resistant to heat,” and "high precision (temperature/voltage control).” The details of these requirements are as follows.
High power
Semiconductor elements making up the BMS need to be capable of handling high power to work with the motor with high power output. High power mentioned here refers to, for example, a case where the current rated voltage of the battery pack, which is about 400 V, is increased to 800 V or higher voltage.
Highly resistant to heat
As electronic components get smaller and smaller, heat per unit area gets higher and higher. Giving an electronic component high resistance to heat prevents its degradation caused by self-heating or incoming heat from components nearby.
High precision (in temperature, voltage)
High power operations go with increasing battery cells and high voltage supply. In such a situation, more precise measurements and control are required.
Circuit configuration of the BMS
Overall configuration
- Battery module:Composed of multiple battery cells connected in series
- Voltage detection circuit (for the battery module):Measures the voltage of the battery module and that of each battery cell
- Monitoring circuit (BMS circuit):Monitors states of respective battery cells and makes cell balance adjustments
- Temperature detection circuit:Measures the temperature of each cell
- Control circuit:Controls the monitoring operation and cell balance adjustment of the BMS circuit
- Current detection circuit:Measures the overall current flow in the BMS
- Voltage detection circuit (for the BMS):Measures the overall voltage of the BMS
- Junction box:Cuts off power supply when a problem occurs, to protect the battery
- Voltage detection circuit (for ground fault detection):Detects a ground fault of the BMS as a whole
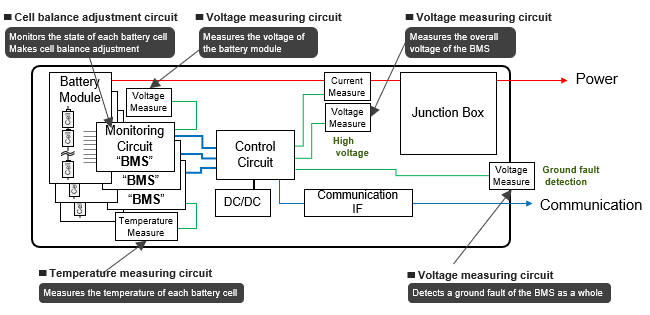
Individual circuits and components
Temperature measuring circuit
When the battery heats to a high temperature, the battery may deteriorate or may even ignite. To avoid such cases, the BMS usually measures the temperatures of the cells, using thermistors (temperature sensors) arranged in the battery module.
Measuring the temperature of each battery cell: NTC thermistor (chip-type)
POINT- ❶ The thermistor is small, highly resistant to heat, and original external electrode forming technology that offers high reliability, thus contributing to highly precise temperature compensation in the circuit.
Cell balance adjustment circuit
Cell balance adjustment is generally carried out in such a way that the voltage of each battery cell is measured to calculate the charge volume of each cell and that surplus charges are released through a resistance to make respective charge volumes of all the cells even.
Discharge: Chip resistor (small and high-power chip resistor)
POINT- ❶ With its original resistance pattern, electrode structure, etc., the chip resistor is small in size and yet handles high-power operations, thus contributing to a reduction in the size of the circuit.
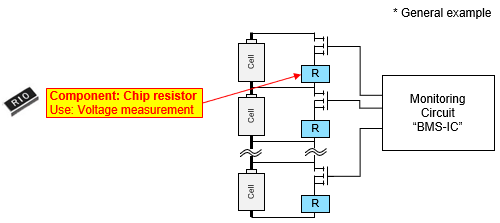
Voltage measuring circuit
Voltage measurement on the battery module and BMS or for ground fault detection requires measurement of high voltage. For this reason, in ordinary situations, multiple resistances are connected to the measurement target and the divided voltage appearing at the resistances is measured.
Voltage measurement on the battery module and BMS unit: Chip resistor (high-precision chip resistor)
POINT- ❶ The chip resistor with a thin-film structure offers a small resistance tolerance and a low TCR, thus contributing to high-precision control of the output characteristics of the circuit.
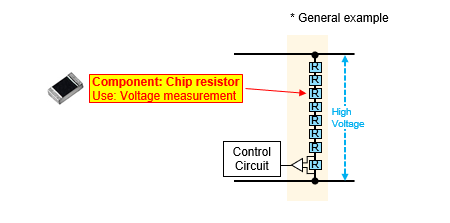
DC/DC converter
In the DC/DC converter, generally, a conductive polymer hybrid aluminum electrolytic capacitor is used to eliminate noise on the input end and to smooth voltage output from the output end, and an in-vehicle power inductor is used for voltage conversion.
Noise elimination, switching, and smoothing: Conductive polymer hybrid aluminum electrolytic capacitor
POINT- ❶ The capacitor offers high capacitance, low ESR, and high ripple-suppression performance, thus contributing to a reduction in the size of the circuit and an increase in the power capacity (low voltage and large current) of the circuit.
- ❷ Having capacitance characteristics to cut off high-frequency components, the capacitor eliminates high-frequency broadband noises that are generated by the high-frequency switching of the circuit.
Voltage conversion: Power Inductors for Automotive application
POINT- ❶ The inductor made of a metal magnetic material allows less power loss and carries a large current, thus contributing to a reduction in the size of the circuit and an increase in the power capacity (low voltage and large current) of the circuit.
- ❷ Having loss characteristics in a higher frequency range (low ACR), the inductor contributes to the suppression of power loss caused by high-frequency switching of the circuit.
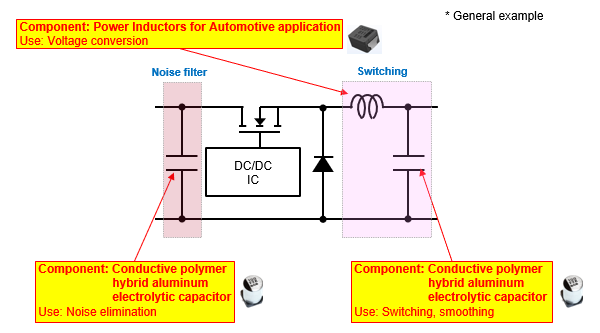
Communication I/F
The communication I/F circuit communicates with external equipment (CAN, Ethernet, etc.) through two communication lines. If noise or static electricity enters via these communication lines, it may cause a transceiver IC to fail. To prevent such problems, the transceiver IC is usually provided with chip varistors serving as electrostatic control measures.
ESD noise elimination: Chip varistor
POINT- ❶ With a wide range of capacitance characteristics, the chip varistor suppresses electrostatic discharge (ESD) noise while keeping the communication quality of the circuit intact.
- ❷ With its capacitance ranging from 8 pF to 250 pF, the chip varistor operates effectively at low to high communication speeds.
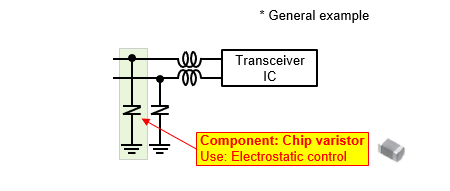
Summary
The BMS is an important system that monitors and controls the state of the battery. With this function, the BMS optimizes the performance of the battery while ensuring its safety. As more and more EVs are produced, more and more BMSs are expected to be incorporated in EVs. Besides, there is a growing demand for motors with high power output, large power capacity and shorter charging time. To meet these requirements, it is essential that the electronic components making up the BMS have these properties: "high power,” "highly resistant to heat,” and "high precision (temperature/voltage control).” Panasonic Industry offers a wide variety of products for use in the BMS (Table 1).
Component | Feature | High voltage | Large current | High heat resistance | High precision |
---|---|---|---|---|---|
![]() |
High precision, high resistance to heat | ✔ | ✔ | ✔ | |
Power Inductors for Automotive application ![]() |
Large current, low loss High reliability |
✔ | ✔ | ||
Conductive polymer hybrid aluminum electrolytic capacitor![]() |
Low ESR High reliability |
✔ | ✔ | ✔ | |
Chip varistor![]() |
Small and light | ✔ | |||
NTC thermistor (chip-type)![]() |
Small, high resistance to heat | ✔ | ✔ |