VRPS (Virtual Robot Programming System) Overview
VRPS is a solution that provides Virtual Robot Programming to a real workpiece by intuitive operations using a VR device.
It requires a special skill and takes time.
It lowers the specialty requirement and reduces time.
VRPS (Virtual Robot Programming System) Features
Virtual Robot Programming System with intuitive operation is realized by the VR (Virtual Reality).
G3/WG3/WGH3 model series
- With the VR technology, it reproduces welder's motions by a robot.
- With intuitive operation, it lowers required programming specialty
- It reduces programming time.
* The VR device is specified by Panasonic
Customer Benefits
Benefit #1 : Virtual Robot Programming
It registers programming points of the real workpiece with the VR device, and enables even unskilled robot operators to perform the robot programming easily.
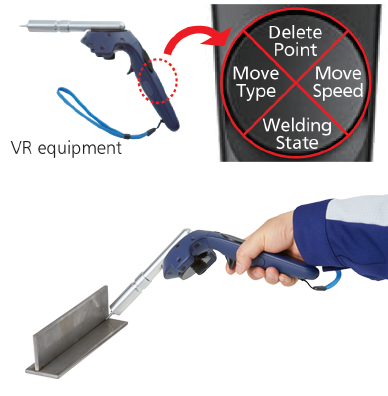
Benefit #2 : Programming Time Reduction
It reduces up to 60% programming time on a complicated workpiece that has many programming points. (own research)
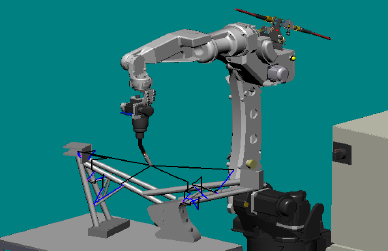
Programming point : Approximately 80 points (Welding section : 30points)
Programming method | Programming time | Correction time*1 | Welding command edit | Total |
---|---|---|---|---|
Actual machine*2 | 2hrs (90sec/point) | none | - | 2hrs |
Offline software | 1hr (45sec/point) | 30min | - | 1h 30min |
VRPS | 7min (5sec/point) | 30min | 10min | 47min |
*1 Assume an on-site correction takes 1m/point, thus 30minutes for 30 points.
*2 Assume an experienced robot operator for the actual machine programming.
How to Use
1. Set up the VR devices
Set the space range where operators move around
2. Synchronize with a real space
Program the basic three points by actual machine.
Synchronize the basic three points using the VR device.
3. Execute a programming
Using the VR device, an operator performs programming by hand with handling welding torch
4. Send the program
The programming is sent from PC to a robot
5. Verify and adjust by tracing
Confirm the actual trace of the programming.
Adjust the programmed points by pitch motions and so on.
System Configuration
A PC and the VR devices are set up by the customers.
Our Product YA-AVPCV1
1. Software (CD-ROM)
2. License key (USB dongle)
3. Torch model
Customer Preparation Items
4. PC (Higher specifications than what we specify)
OS : Windows 10 64bit
CPU : Intel® Core™ i5-4590 equivalent or above
GPU : NVIDIA® GeForce® GTX 1060 equivalent or above
Memory : 4 GB or more
Video output : DisplayPort 1.2 or later
USB port : USB 3.0 or later, 2 ports or more
5. HTC VIVE Pro
(Our specified device, See HTC co. website for details) headset, base station (sensor) ×2 controller×2, HDMI cable, USB cable
6. LAN cable
7. Sensor stand
Precautions upon a purchase
Please make sure to read the precautions below before purchasing a VRPS.
Applicable machine
- It is applicable to CO2/MAG/MIG machines. In case a TCP adjustment is properly done, it can be applied to non-standard torches.
However, please check beforehand if it interferes with the workpiece or jigs with the actual machine.
Inapplicable machine
- It is not applicable to the TIG or CUT.
- It is not applicable to a positioner or does not support collaborative motion.
Out of Warranty
- Defects caused by operating a VRPS other than those described in the operating instructions.
- Defects caused by using a VRPS outside.
- Misaligned programming points caused by vibration of equipment or buildings.
- Misaligned programming points caused by a “strong light (including arc light) " or "noise" cluttering the infrared.
- Misaligned programming points caused by dirt on a VR device base station or a controller (it interferes the accuracy of infrared sensing).
Precautions for the VR device
- The VR device will not has a product warranty as it is for the commercial use. Please register “VIVE Enterprise Commercial Warranty Certification". It will be a separate cost to the customers (available within Japan only).
- As for the VR devices and the PC, please make sure to confirm the specifications.
- The VR devices and the PC are to be set up by the customers. Obtain a separate quote if a set up service is needed.
- Four to six 100V electric outlets will be needed. Have them ready.
- Do not perform welding nearby a running VRPS. The infrared in a welding arc light may cause a malfunction.
Precautions for the programming point
- Position accuracy : There will be a misalignment. Perform an operation check and position correction before operating the machine.
Programming correction is mandatory. - In order to improve position accuracy :
- Retain head mount display tracking while programming.
- Run the VR devices at least 30 seconds prior to performing a programming or calibration.
- Adjust the robot TCP properly.
- Perform the TCP adjustment of the torch model attached to the VR device.
Limitations of the operating environment
- Do not generate “strong light (including arc light) or “noise" that disturbs the infrared rays of the sensor.
- In case of using multiple VR systems, it is necessary to prevent interference to infrared by using a plate or so on.
Limitations of the operating environment
It is not applicable to a workpiece that does not fit in the programming area.
Programming area floor size
Max : 10m × 10m *1 (Diagonal Length 8m) Min : 2m × 1.5m (Diagonal Length 2.5m)
*1 When using 4 sensors (base stations) used, It is 5m×5m when using 2 sensors.
Limitations of Sensing
- Make sure two infrared rays reach the VR device during a programming.
- As for the sensor setting height (base station), 2m or higher is recommended (up to 3m).
Related information