ESD(静電気放電)対策の基本と試験プロセス
2025-3-28
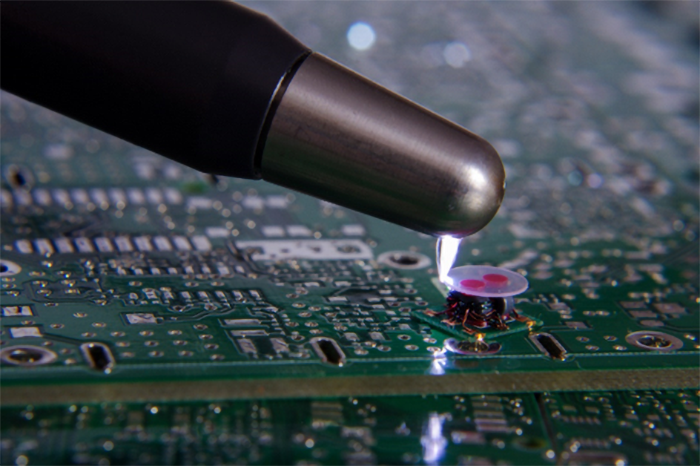
自動車の電子化が進む中で、ESDは重大な課題となっています。静電気は目に見えないレベルでも発生し、半導体デバイスの破壊やシステムの誤作動を引き起こす可能性があります。特にCASE時代において、ECUや集積回路の増加に伴い、ESDの影響はより深刻になります。本記事では、自動車におけるESD対策の重要性を解説し、静電気を安全に逃がすための技術や評価手法について詳しく紹介します。
1. ESD(静電気放電)対策とは
自動車の安心安全を脅かすストレスは多岐に渡ります(図1)。そのストレスのひとつであるESD(Electrostatic Discharge:静電気放電)は、物体や人体に蓄積された静電気が急激に放電される現象を指します。この放電は目に見えないレベルでも発生し、電子機器に深刻なダメージを与えることもあります。例えば、半導体デバイスの破壊、電子回路の誤作動、データの損失などが発生する可能性があります。特に、車載電子機器や精密機器ではESDによる影響が大きいため、適切なESD対策が不可欠です。
ESD対策は「機器を静電気から守る」ことを目的としており、大きく分けて「静電気の発生を抑える」、「静電気を安全に逃がす」という2つのアプローチがあります。本レポートでは主に「静電気を安全に逃がす」ためのデバイスについてご紹介します。
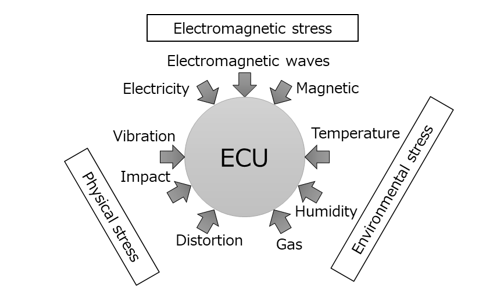
2. CASE時代に求められるESD対策
2-1. CASEとは
CASEは、「Connected(接続)」「Autonomous(自動運転)」「Shared(共有)」「Electricity(電動化)」の頭文字を組み合わせた造語であり、自動車産業の技術革新を象徴するキーワードです。これら4つの要素が互いに連携することで、自動車のあり方が大きく変わりつつあります。従来のガソリン車やディーゼル車といった内燃機関(ICE)を主体とした時代から、より高度な電子制御技術を駆使したスマートモビリティへと移行しているのが現在の自動車産業の潮流です。
この技術革新により、自動車は単なる移動手段ではなく、情報をリアルタイムで処理する「デジタルデバイス」としての役割を持つようになりました。特に、自動運転技術や電動化の進展により、車両内部には高度な電子制御ユニット(ECU)や集積回路(IC)が多数搭載され、これらの安定した動作が車両全体の安全性に直結するようになっています。しかし、こうした電子機器の増加に伴い、ESD(静電気放電)による影響が重要視されています。
2-2. なぜESD対策が必要か
電気自動車(BEV)や燃料電池自動車(FCEV)などでは、車両の駆動系や制御系がすべて電子機器によって管理されているため、ESDによる影響がより直接的な問題となってきます。
例えば、高電圧のESDがICやECUに加わると、モーターの制御が不能になり、最悪の場合、車が走行不能に陥るリスクがあります。また、ESDは瞬間的なものであるため、システムの誤動作や不安定な動作を引き起こす可能性もあります。さらに、メモリデバイスに影響を与え、車両データの消失や誤作動を招くことも考えられます。
このように、CASEによる技術革新が進むほど、ESD対策は自動車の安全性と信頼性を確保する上で欠かせない要素となります。車載電子機器が増加する中で、ESDの影響を最小限に抑えるための対策が求められています。
3. ESD対策部品の評価手法
3-1. 主な評価規格(IEC 61000-4-2 / ISO 10605)
部品の耐性と性能を正確に把握するために評価を実施します。標準化された評価手法として認められているIEC 61000-4-2やISO 10605などの規格に沿って評価が行われます。これらの規格では、部品単体のデバイスレベルだけでなく、より実際の使用環境に近いシステムレベルでの評価がされます。
実際の評価では、表1に示す容量と抵抗を組み合わせたESDシミュレータを使用し、接触放電法によって高電圧が印加されます。図2に150pFの容量と330Ωの抵抗を組み合わせたESDシミュレータの回路構成を示します。この方法によって、部品やシステムがどこまでの電圧に耐えられるのか、さらにどのような故障モードが発生するかを確認します。
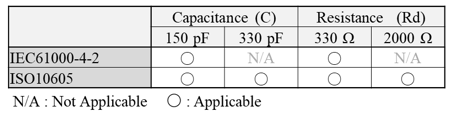
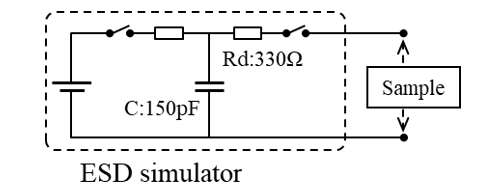
3-2. ESD電圧ステップアップ試験と繰り返し印加試験
ESD試験の基本的な試験プロセスは図3の通りです。まず、初期測定として試験前の諸特性を測定した後、各試験の設定試験レベルに従いESDを印加します。
ESD電圧ステップアップ試験と繰り返し印加試験は、ESD耐性を評価するために実施します。ESD電圧ステップアップ試験では、電圧を段階的に上げていき、部品が耐えることができる最大電圧を特定します。
一方、繰り返し寿命試験では、同一の電圧を複数回印加して、部品の劣化や耐久性を評価し、どの電圧レベルから不具合が発生し始めるかが把握できます。
これらの試験を組み合わせることで、実際の使用環境下で部品がどの程度ESDの影響を受けるかを確認し、最適な対策を検討できます。
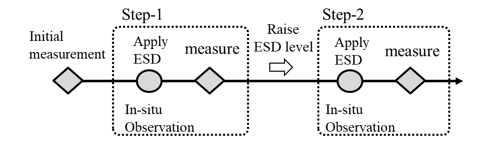
3-3. 可視化カメラでの放電現象観察
今回使用したESD可視化カメラは(株)ブルービジョン製のBV‐C2950です。その仕様概要を表2 に示します。このESD可視化カメラを使用すると、放電現象をリアルタイムで可視化できます。このカメラは近紫外線を捉える機能を持っているため、通常は目に見えない端子間放電といった現象を記録できます。また、低電圧での放電も捉えられるため、不具合箇所や発生タイミングを正確に把握する手段として有効です。放電が発生する具体的な場所や時間を正確に特定できるため、故障の原因分析や設計の改善に非常に役立つツールとなります。
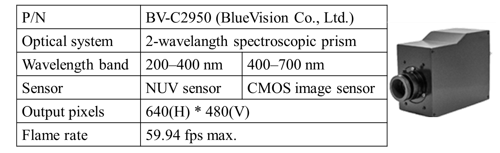
4. 試験結果と考察
4-1. 試験対象
本レポートでは車載機器のESD対策部品としてMLCC(Multi-Layer Ceramic Capacitor:積層セラミックコンデンサ)とMLCV(Multi-Layer Ceramic Varistor:積層セラミックバリスタ)を対象として図2に示す構成のESDシミュレータでESD試験を実施し、それらの性能評価を行っています。MLCCは車載機器で従来からESD対策に使われており、MLCVはSI(Signal Integrity)確保に優れているということでCAN(Controller Area Network)等の車載インターフェースにおいて近年使用されるようになってきています。いずれもセラミック積層電子部品です。
4-2. MLCCの特性変化
図4は放電異常と特性異常(静電容量変化率やショート故障)の観点から、ESDに対する許容レベルを安全領域としてマップ化したものです。MLCCの特性は、8kV以上のESDが印加された時に顕著な変化が見られました。この高電圧での試験では、端子間や内部で放電が発生しやすくなり、特に小容量や小型のコンデンサでは耐性が低下する傾向があります。さらに、ESDが繰り返し印加されると、コンデンサ内部でのショート故障や、リーク電流の増加が確認できました。
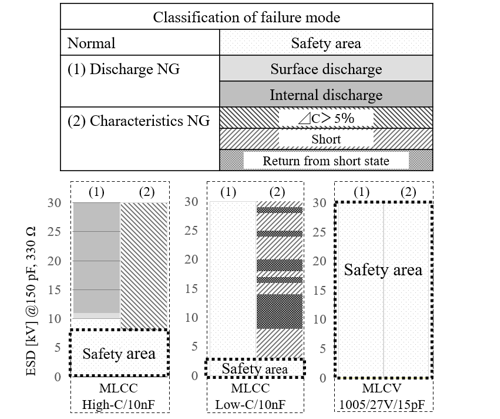
(ΔCはESD試験前後の静電容量の差)
4-3. MLCVの高耐性と放電なしの利点
図5はMLCVの抑制電圧を比較した結果です。MLCVは、30kVという高い電圧まで端子間放電や故障が発生せず、ESDに対して非常に高い耐性を持っていることが分かりました。これにより、高電圧の影響を受ける状況でも安定したパフォーマンスを維持できます。また、抑制電圧が低く保たれるため、回路に与える影響を最小限に抑えられます。以上のことから、MLCVは高いESD耐性と安定した抑制電圧を兼ね備えており、車載電子機器の保護に最適です。
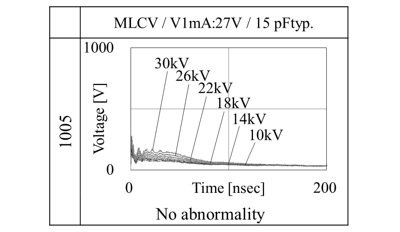
5. まとめ
ESDは、車載電子機器に深刻な影響を与える要因のひとつです。特に、電気自動車や自動運転車の普及に伴い、ESD対策の重要性は増しています。本記事では、ESD試験の評価規格(IEC 61000-4-2 / ISO 10605)に基づく試験プロセスや、ESD可視化カメラを用いた放電現象の観察について紹介しました。
次回記事では、MLCV単独使用によるESD対策や、MLCCとの並列構成によるノイズ抑制の効果など最適な回路構成について紹介します。