Bead Eye (Visual Weld Inspection Solution) Overview
Bead Eye is a solution that provides “labor-saving" and “enhanced traceability" by automating the manual visual inspection.
Scanning weld beads
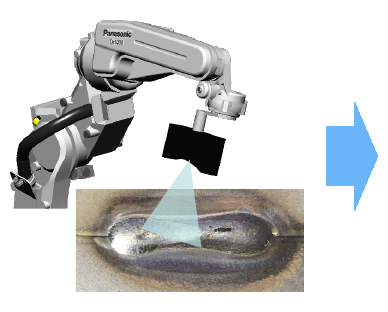
The scanner attached to the robot scans bead shapes.
Inspection judgement
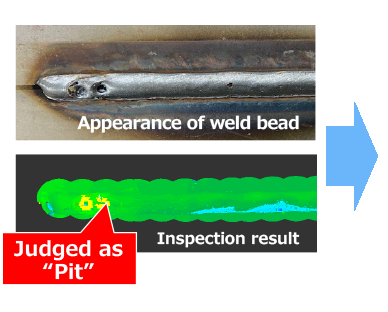
Logic #1 : Master Compare Inspection
Logic #2 : AI (Visual) Inspection
Traceability
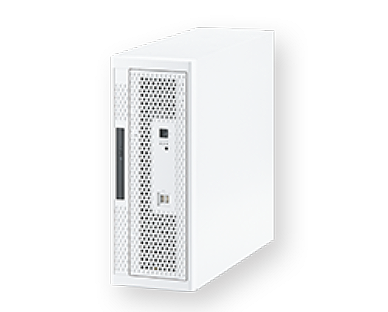
Inspection result data is stored in the industrial PC
BeadEye (Visual Weld Inspection Solution) Features
Inspection Logic #1: Master Compare Inspection
Setting up is easy because it is a compare inspection to the master data.
It compares the target products to the pre-set master data, and judges pass/fail based on the concordance rate.
*Please read the and other details here.
Inspection logic #1: Limitations of master comparison inspection
- This inspection can not determine the type of welding defects, nor calculate design values such as bead leg length.
- Defects that hardly show changes on the concordance rate (e.g. spatter, extremely small holes) may not be detected.
- If the inspection location is out of the measurable range of the sensor, a part of point group data may be missing and the inspection may not be performed correctly.
- It can not judge defects where the sensory laser beam penetrates through (e.g. holes).
* The above limitations are on a case-by-case basis. Pre-confirmation is always required even if it is within the scope of above limitations.
* Defects that are impossible to judge from the bead geometries, such as internal defects or insufficient penetration can not be detected.
Inspection Logic #2: AI (Visual) inspection
The AI engine that pre-learnt at Panasonic will not miss those welding defects that were difficult for automatic visual inspection before.
AI learns the shape of the defects and judges its type and position. It can inspect the smallest defects easily.
* The AI engine installed in this system is already done its learning. Additional AI learning, etc. can not be performed by customers.
*Please read the and other details here.
Inspection logic #2: Limitations of AI inspection
- If multiple defect factors overlap, only one of them may be detected.
- If multiple welding defects are too close, different types of defect may be detected as one.
- Demonstration using an actual workpiece and jigs is required. (For the individual detection range of a defect, please consult us.)
- AI inspection is only applicable to the straight (not curved) weld bead.
- It is applicable only to arc welding.
- It supports only the joints with the following shapes:
(1) overlap fillet joint (2) T-shaped fillet joint, and (3) butt joint. Please contact us for flare fittings, etc. - It is not applicable to scale-shaped bead.
* The above limitations are on a case-by-case basis. Pre-confirmation is always required even if it is within the scope of above limitations.
*Defects that are impossible to judge from the bead geometries, such as internal defects or insufficient penetration welding, can not be detected.
Customer Benefits
Defect | Master Compare | Chipping of bead | Out-of-line bead | Over/under filling bead | Over/under bead width | Over/under bead length | Hole | Pit | Undercut | Spatter |
---|---|---|---|---|---|---|---|---|---|---|
Inspection Logic | ||||||||||
#1 Master Compare Inspection |
![]() |
![]() |
![]() |
![]() |
![]() |
![]() |
||||
#2 AI inspection |
![]() |
![]() |
![]() |
![]() |
||||||
BeadEye (#1+#2) | ![]() |
![]() |
![]() |
![]() |
![]() |
![]() |
![]() |
![]() |
![]() |
![]() |
System Configuration
Provides a total weld bead inspection equipment except for the robot.
System configuration example (TM-1400G3)
Precautions upon purchase
Please make sure to read the precautions below before purchasing Bead Eye.
- Applicable models are TM/TL/TS/ LA-series robots connected to G3 or TAWERS (WG3 / WGH3) type controller.
Please contact your nearest sales office for details. - This inspection function is only to inspect welding beads of CO2/MAG welding using mild solid wire. It is not applicable to other purposes, such as inspection for TIG welding and laser welding.
Also, it is not applicable for cases that cause a significant color change on the bead surface e.g. galvanized steel sheet. - It is possible to install a work for measurements on a positioner or the like only if the positioner or the like is in a still state. It is not possible to perform inspection if the harmonic movement function is used.
- It is not possible to detect defects that are not identifiable from the welding bead shape, such as internal defect and insufficient penetration.
- This inspection function is capable of performing ideal inspection by conducting various settings and teaching suitable to the applied work, processing conditions and production facilities. This product does not guarantee the quality of the inspected work. User of this product should guarantee the final quality of the work.
- It cannot be used in an environment where strong ambient light, such as CO2/MAG/ MIG/TIG welding, exists in the same work area.
- This function requires to examine applicability to the user's works at our Process Engineering Center prior to introducing the function. (Only pre-confirmed works and defects are the scope of guarantee.)
- Please contact your nearest sales office for the retail price, contract, operating environment, and customer preparation item details.