"CASE"時代を迎えた自動車のトレンドと技術課題(2)
バッテリー・マネジメント・システム
2019-12-16
今回は、"CASE" 時代を迎えた自動車のトレンドと技術課題の2回目として、CO2排出抑制を背景に世界的にシフトが進む電気自動車(EV)から、バッテリーと、バッテリー・マネジメント・システム(BMS)を取り上げます。
電気自動車(EV)の実用化を加速させたリチウムイオン電池
電気自動車 (EV)はガソリン車やディーゼル車に匹敵する走行性能と航続距離の実現を目指して開発が進められてきました。さまざまな技術開発がEVを後押しする中で、従来のニッケル水素電池に比べて体積エネルギー密度および重量エネルギー密度がともに数倍以上と高いリチウムイオン電池の登場によって、EVの実用化は一気に加速したといえます。
リチウムイオン電池は、一般に、正極にリチウム遷移金属複合酸化物を、負極に炭素材料をそれぞれ使用したものを指しますが、正極ではなく負極にリチウム系酸化物を使用したものもあり、さまざまな材料の組み合わせが実用化されています。
リチウムイオン電池は体積エネルギー密度および重量エネルギー密度ともに優れてはいるものの、ガソリン車やディーゼル車と同等の航続距離を実現するには、従来はかなりの大きさのバッテリーユニットを搭載しなければなりませんでした。しかし現在では、バッテリーの性能向上だけではなくモーターを駆動するパワー半導体の効率向上などもあって、小型EVでも400km(WLTCモード)を超える航続距離が謳われるまでになっています。
安全な充放電制御に欠かせないバッテリー・マネジメント・システム(BMS)
EVに搭載されるバッテリーの性能を引き出す役割を担うのがバッテリー・マネジメント・システム(BMS)です。電子回路とソフトウェアで構成されていて、主に次の二つの機能を備えます。
- 過電圧、過電流、異常発熱などの検出と遮断制御
- 充電制御や残り航続距離の目安となる電池残量(充電状態:SOC=State of Charge)の推定
リチウムイオン電池は、満充電電圧を超えての充電や終止電圧を超えての放電は異常発熱などにつながる恐れがあるため、SOCの正確な把握は安全な充放電管理にも必須といえます。
また、BMSはオプションとして次の機能も担います。
- バッテリー・セルの充電状態を揃えてバッテリー・パックの容量を最大化するセル・バランシング制御
このうち、BMSの基本機能のひとつである(2)について説明します。
バッテリー・パックの充電状態(SOC)を推定する方法
ガソリン車やディーゼル車では燃料タンクのフロート(浮き)の高さによって燃料の液面を物理的に把握することができますが、対してEVの場合はバッテリー・パックにどのぐらいのエネルギーが蓄えられているかを外部から知ることができないため、専用の回路とアルゴリズムを用いて「推定」を行わなければなりません。
SOCを知るには大きく二つの方法があります。
(a)バッテリー・セルの電圧を計測する方法
(b)バッテリー・パックの入出力電流を積算する方法
(a)バッテリー・セルの電圧を計測する方法
まずセル電圧からSOCを知る方法を説明します(図1)。
バッテリー・パックを構成するそれぞれのバッテリー・セルの両端電圧をADコンバータで読み取って、SOCの推定ロジックに与えます。また、セル電圧は温度によって変動するので、バッテリー・パックの温度も計測し、合わせてSOC推定ロジックに与えます。
ただし、バッテリー・セルの個数だけADコンバータを用意するのはコスト的にも実装的にも無駄が多いので、通常はマルチプレクサをADコンバータの前段において、一定周期でスキャンしながら計測していきます。
セル電圧を計測するADコンバータには高速性はそれほど求められませんが、後述のように数mVの精度が必要ですので、10ビット以上のENOB(有効ビット数)を比較的容易に確保できるΔΣ型が用いられる場合が多いようです。
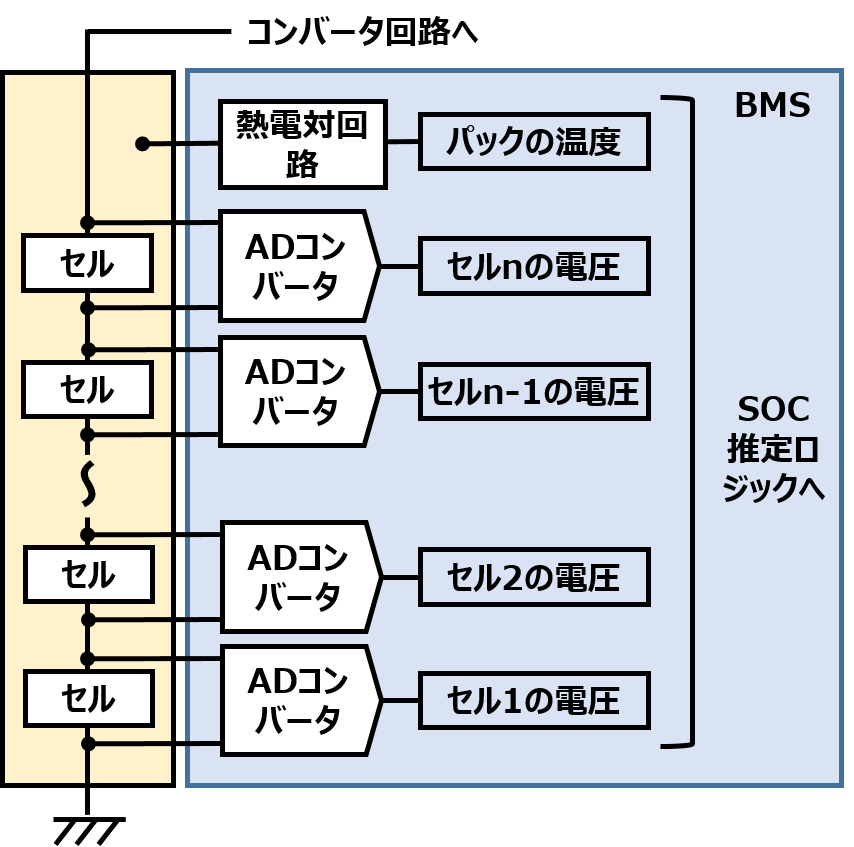
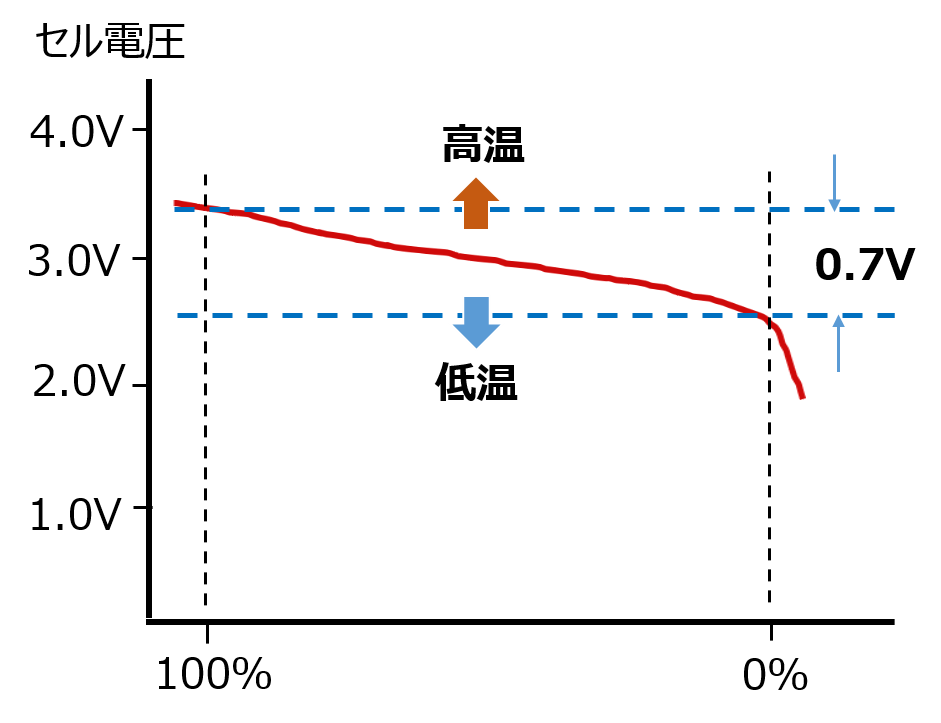
正極と負極に使用する材料にもよりますが、一例として、満充電時の電圧を3.4V、終止電圧を2.7Vとします(図2)。
つまり、3.4Vのときを100%、2.7Vのときを0%として、セル電圧からSOCを算出すればいいことになります。ただし、SOCを1%単位で算出するには0.7÷100=0.007V (7mV)という高い精度でセル電圧を計測しなければなりません。実際には、セル電圧は温度係数を持ち、高温になると上昇し、低温になると低下します。とくに走行中と充電中(回生ブレーキ含む)は流れる電流に応じて温度が変動するため、電圧も微妙に変動し安定しません。セルやパックの温度からある程度の補正はできるものの、安定していない状況下では高い計測精度を保つことは大変難しいとされています。
こうした制約から、セル電圧を計測してSOCを求める場合は、相応のマージンを設定する場合が多いようです(たとえば±10%の計測誤差を見込んで、実際の10%~90%を0%~100%として表示するなど)。
(b)バッテリー・パックの入出力電流を積算する方法
(b)は、セルに流出入した電流を積算し、セルに残っているであろう電荷 ( エネルギー ) からSOCを求める方法です(図3)。
この方法は、クーロン・カウンティング法とも呼ばれます。たとえば、バッテリー・パックの容量が1000Ahrとして、10.0Ahr相当の電荷が流れたと計測された場合、SOCは1.00%減少したと求められます。逆に10.0Ahr相当の電荷が充電された場合は、SOCは1.00%増加したと求められます。
μΩオーダーのセンス抵抗(バス・バーなど)の両端電圧をA/Dコンバータで変換し積算していきますが、誤差の蓄積を抑えるには、有効ビット数がそれなりに多く、かつ、変動を捕捉できるようにサンプリングレートがある程度高速なことが必要です。
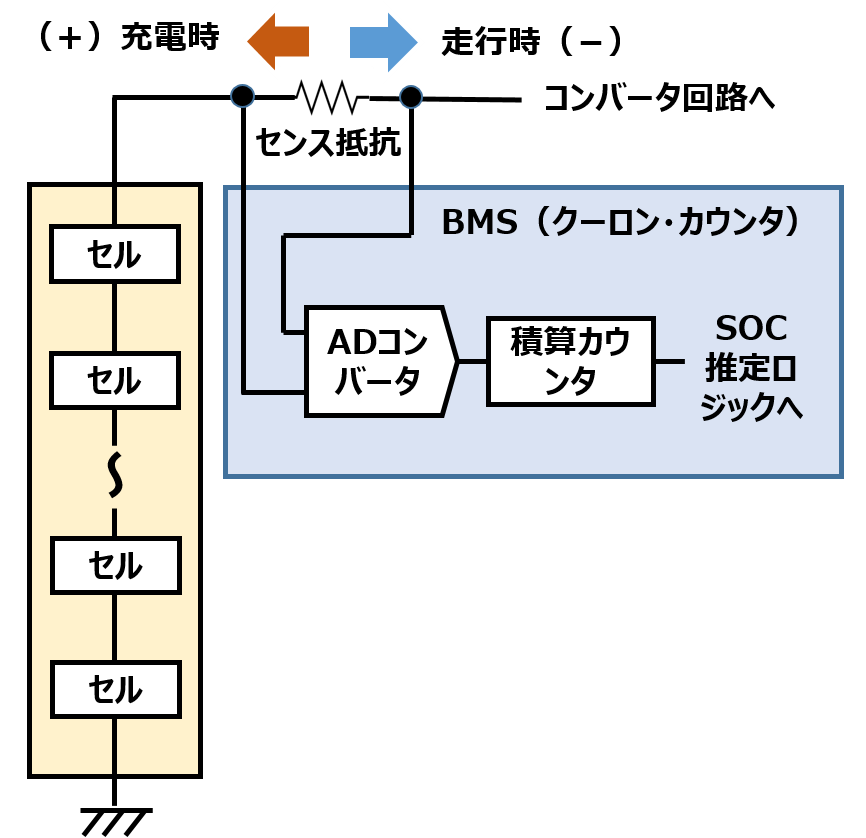
ただし、前述で説明した(a)と(b)の方法はあくまで机上での話であり、実際はセルの経時劣化(SOH:State of Health)なども加味しながらSOCを求めていかなければなりません。実装は自動車メーカーによって異なり詳細は明かされていませんが、図1や図3のような手法で計測した電圧や電流などの情報を使いながら、カルマン・フィルターなどの数学的手法を用いてSOCを推定していると考えられます。
なお、BMSの基本的な役割として示した「(1) 過電圧、過電流、異常発熱などの検出と遮断制御」は、基本的にはセル電圧やセル温度を計測する回路や、バッテリー・パックの流出入電流を計測する回路の延長で実現されます。
バランシング制御でバッテリー性能を最大化
リチウムイオン電池は充放電を繰り返しているうちに少しずつ劣化が進んでいきます。バッテリー・パックを構成するすべてのセルが等しく劣化すれば問題は少ないのですが、実際にはバラつきが生じます。
バッテリー・パック内でバッテリー・セルは図1や図3のように直列に接続されますが、模式的に、図4のようにセルを並べて考えてみます。
経年変化などによってセルの特性や性能にバラつきが生じた場合、放電においては、残容量(SOC)のもっとも小さいセルが放電下限に達した時点で放電をストップする必要があります(図4左下)。つまり、ほかのセルの赤い矢印で挟んだ部分のエネルギーは利用できません。
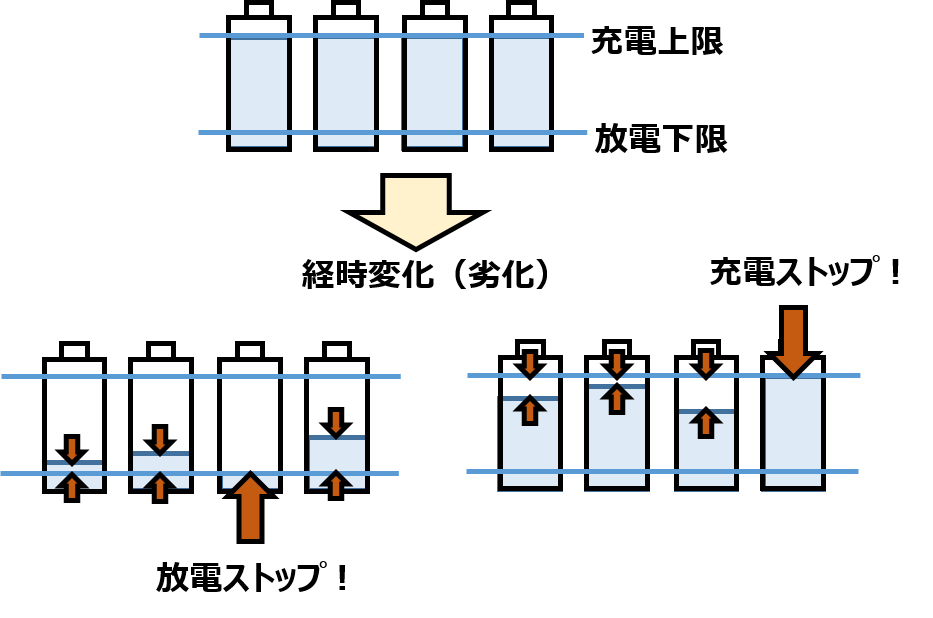
また、充電においては、残容量のもっとも多いセルが充電上限電圧に達した段階で、充電をストップする必要があります ( 図4右下 ) 。ほかのセルの赤い矢印で挟んだ部分には充電できません。
すなわち、ばらつきが生じた一部のセルに律速されて、実効容量は減少してしまいます。
こうしたバラつきを抑えるのがセル・バランシングです。手法としては、残容量の多いセルを抵抗負荷に接続して放電させ、各セルのSOCを放電下限に揃えるパッシブ・バランシングと、残容量の多いセルから残容量の少ないセルにエネルギーを配分するアクティブ・バランシングとがあります。回路はもちろん後者が複雑になります。
進化が続くBMSに引き続き注目
図1や図3にBMSの一部を模式的に示しましたが、実際はもっと複雑で、多くの構成部品を必要とします。小型化を図るべく、これら機能を集積したBMS ICや 回路部品 がさまざまな 電子部品メーカー からリリースされています。
また、SOCの推定を含めて、新しい制御方式が日々開発されています。今回示した従来の考え方はいずれ「古典的手法」に分類されてしまうかもしれません。
バッテリー自体も、新しい正極材料や負極材料の研究開発が進められていて、さらなるエネルギー密度の向上が期待されています。
これからも BMS の普及と進化から目が離せません。
次回はADASや自動運転の鍵となるAIプロセッサについて取り上げます。