熱対策の基礎知識(3)
~熱設計と熱対策~
2019-03-18
はじめに
熱対策は、機器やシステムの特性や寿命、そして安全性を確保するための重要検討事項です。「熱対策の基礎知識」では熱対策を行うための基礎的な知識を、「熱の基礎知識」、「熱対策が必要になる背景」、「熱設計と熱対策」の3回に分けて解説しています。今回は最終回となる3回目、「熱設計と熱対策」です。
熱設計とは
熱設計とは、熱シミュレーション等によって製品設計の段階で必要な熱対策を盛り込むことを言います。
昔の電気製品は十分なスペースを持って部品が配置されていたので、製品開発の最終段階で熱対策の必要性を検証すれば済みました。しかし近年は、機器の小型化や高性能化にともなって設計段階で熱対策を設計に盛り込むことが重要となっています。
例えば、事前に寸法が決まっている機器において、最終評価段階で熱対策が必要となり、急遽ファンを取り付けることになったら、ファンを入れるためのスペース確保のため、回路設計を一から見直すことになり、場合によっては企画そのものが中止となることもあります。
しかし、設計段階で熱シミュレーションを実施し、機器の温度分布を把握し、熱対策を行えば効率的な製品開発が可能となります。
熱設計のプロセス
熱設計は大まかに言うと、上限温度条件の設定、部品部材の発熱・熱伝導特性調査、熱シミュレーションの実施、熱対策の検討の4つのプロセスで進めますが、シミュレーション結果が設定温度以下にならなければ適切な熱対策を検討し、その熱対策を盛り込んで再度シミュレーションを行い、これを設定温度以下となるまで繰り返します。
但し、この熱シミュレーションは精度が高いとは言えず、また対策内容をシミュレーションに盛り込むことが困難な場合もあるので、最終的には実機による温度測定によって対策を確定させる必要がありますが、熱設計をしない場合と比べれば、最終評価段階での回路設計見直しというリスクは遥かに小さくできます。以下にそれぞれのプロセスを説明します。
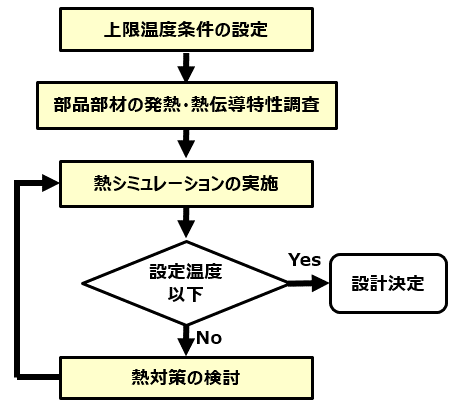
上限温度の設定
機器周囲温度の上限設定
機器の周囲温度によって機器の内部温度は大きく影響を受けるため、機器の使用上限温度は低く設定した方が機器内部の冷却には有利です。しかし、使用者からすれば使用環境の制限を受けない温度設定であることが望ましいと言えます。
そのため、双方を考慮した使用温度範囲を製品仕様としてあらかじめ設定します。
機器内部温度の上限設定
各部品の最高使用温度を調査し、それぞれの部品が最高使用温度を超えないように設定します。
なお、アルミ電解コンデンサのように温度と寿命に強い相関がある部品であれば、寿命を考慮して部品の最高使用温度よりも低い温度設定としなければならない場合もあります。
機器表面温度の設定
モバイル機器など、高温になるとやけどに繋がる可能性がある機器は、機器の筐体表面温度も規定する必要があります。
部品部材の発熱・熱伝導特性調査
機器の動作条件において、各部品がどの程度発熱するかを確認する必要があります。
電子部品が動作するとエネルギー損失により発熱し、機器が温度上昇します。特にCPUやパワー半導体などは大きな発熱を生じるため最も注意が必要な部品です。
また、基板や筐体などの部材も含めて各種熱伝導特性(熱抵抗、熱放射率等)も調査する必要があります。しかしこれら熱伝導特性は把握するのが難しい場合が多いので、都度調査するのではなくデータベース化しておいて流用することで手間が省けます。
熱シミュレーションの実施
熱シミュレーションは、前記の温度条件・熱特性の前提条件において、部品の配置、風の流れによって各部位の温度がいくらになるかをシミュレーションするものです。
この計算はエクセルベースでも可能ですが、専用の熱流体解析ソフトも多く出ていますので、それらを活用した方が容易に解析できます。
熱対策の検討
- 部品配置の見直し
- 筐体材質を見直し
- 風穴や冷却ファンの設置
- ヒートシンクの取り付け
- ヒートパイプの取り付け
- 断熱シートの取り付け(発熱部品と低耐熱部品間)
- TIM(熱界面材料)の採用(発熱部品とヒートシンク間)
これらの熱対策を行った場合に各部位の温度がどのように変化するかを再度熱シミュレーションによって計算します。
熱対策の手段
前項で熱対策の項目を列記しましたが、ここではそれぞれについてもう少し詳しく説明します。
部品配置の見直し
発熱部品が風上にあると、他部品への熱影響が大きくなるので、発熱部品はなるべく風下に設置すべきです。
また、熱に弱い部品は発熱部品から遠ざける、冷却を考えた空気の通り道をつくる、等も有効です。
筐体材質の見直し
機器内部の熱は機器の筐体(ケース)を通しても外気に放熱されます。
そして、その放熱量は筐体材質の熱抵抗によって大きく異なり、例えば熱抵抗の高いプラスチック製の筐体であれば放熱量が少なく、熱抵抗の小さいアルミ製の筐体であれば放熱量が大きくなります。
このように筐体を熱抵抗が小さい材質に変更すれば冷却効果が高くなります。
また、筐体は表面積が大きいのでヒートシンクの代替品として使うことができ、発熱部品を筐体に密着させて放熱させるという手段も有効です。
風穴や冷却ファンの設置
筐体上部に風穴を設けただけでもある程度の冷却効果はありますが、さらに冷却ファンと併用すれば大きな冷却効果が得られます。この場合、筐体内部の冷却効果が高くなる風の通り道を考えて設置場所を決定します。
なお、冷却ファンの設置は、スペースの確保や騒音の増加、消費電力の増加という課題も発生するので、その課題が容認できない場合は使用できません。
ヒートシンクの取り付け
ヒートシンクは、吸熱, 放熱を目的として発熱体に取り付ける部品で、放熱器や放熱板とも呼ばれます。伝熱性能の高いアルミニウム、鉄、銅などが材料として利用されることが多く、伝熱面積拡大のために多数のフィンを持つ構造が一般的です。ヒートシンクは放熱面積の拡大には有効な部品ですが、比較的重量がありサイズ(体積)も大きいので、その使用する場合には十分な空間が必要になります。
なお、発熱体とヒートシンクの接合には熱伝導を高めるための熱界面材料TIMを使用するのが一般的です。
ヒートパイプの取り付け
密閉した特殊なパイプの中に揮発性の高い液体を封入したもので、熱を拡散するために使用し、熱の拡散効果が高いのが特長です。右図は、ヒートパイプの熱拡散の原理を説明した図です。ヒートパイプ内の作動液は高温部の熱を吸収して蒸発し、その蒸気は低温部に移動します。すると蒸気は低温部で放熱して液化します。そして液化した作動液は還流します。このサイクルを繰り返すことで熱を拡散します。
代表的な応用例としては、CPUクーラーが挙げられます。
断熱シートの取り付け
熱に弱い部品は発熱部品から遠ざける必要がありますが、回路設計上困難な場合には両者の間に断熱シートを取り付けて熱に弱い部品を保護する対策が有効です。
また、モバイル機器などで筐体表面温度を抑制する必要がある場合にも、筐体と発熱部品の間に断熱シートを取り付ける対策が有効です。
TIM(熱界面材料)の採用
発熱部品の熱をヒートシンクで冷却するとき、両者の接合面に隙間があると接触熱抵抗が高くなり、効率の良い冷却ができません。そこで、発熱部品とヒートシンクの接合面の隙間を熱抵抗の低いTIMで埋めることで冷却効果が高まります。
以下に、代表的なTIMを紹介します。
サーマルグリース
サーマルグリースは、発熱体とヒートシンク間に塗布して使用するTIM材で、古くからある最も一般的かつ安価なTIMです。しかし均一に塗布することが難しく、また長期信頼性に課題を持ちます。
熱伝導シート
熱伝導シートは熱伝導性に優れたシート状部材で、発熱体とヒートシンク間に挟んで使用するTIM材です。種類としてはシリコンシート、エラストマーシート、グラファイトシートなどがあり、サーマルグリースを代替可能です。取り扱いが容易ですが、良好な接触を得るには接触圧が必要になります。
PCM (フェイズチェンジマテリアル)
PCMは高温下で軟化する低熱抵抗材料で、発熱体とヒートシンク間に挟んで使用するTIM材です。高温での軟化により密着性が向上し、接触熱抵抗が低減することを特長とします。シート状で取り扱いが容易ですが、コスト面が課題です。
まとめ
熱設計とは、熱シミュレーション等によって製品設計の段階で熱対策を盛り込むことです。これにより、回路設計と合わせた効率的な設計が可能となります。
熱シミュレーションおよび熱対策にはそれぞれ適したアプローチがあり、それを実現するために様々な方法と部材が用意されています。熱対策を行うには、部材の特徴を理解し性能を比較検討した上で適材を適所に採用します。
「熱対策の基礎知識」は今回で最後になりますが、別途、優れた性能を持つTIMによる課題解決事例の紹介を予定しています。