What is LiDAR/Radar?
- LiDAR (Light Detection and Ranging or Laser Imaging Detection and Ranging)
- Radar (RAdio Detection And Ranging)
LiDAR is the technology to measure the distance to the obstacles with infrared laser light.
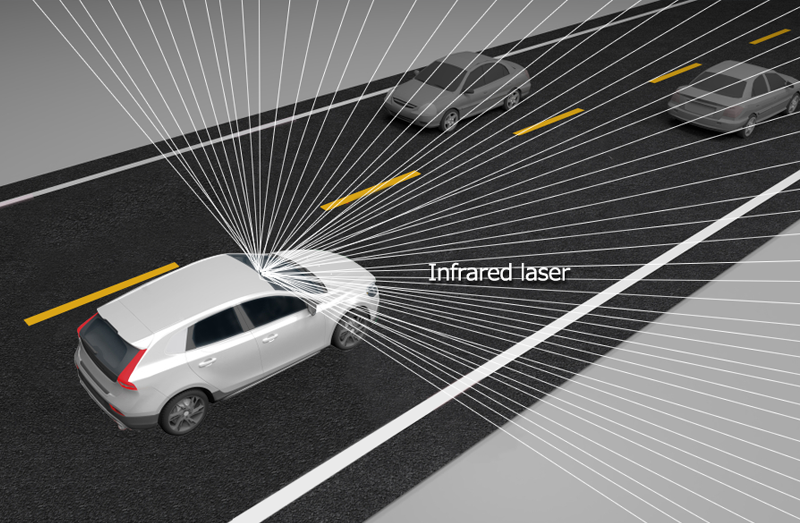
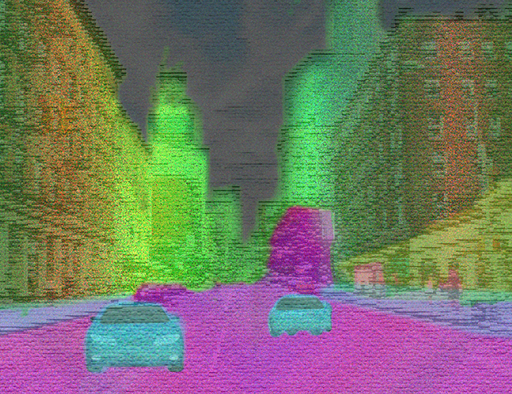
Radar detects the obstacles and measures the distance with the milimeter wave reflections.

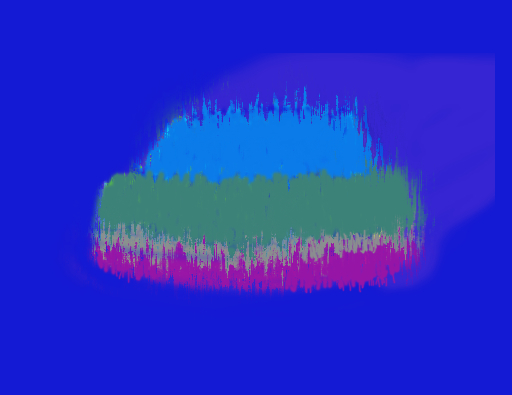
What are the positives to use 6in1 sensor for LiDAR/Radar?
1 : Realize the detection of installation offset and inclination
Usually, there are cases where mounting offsets occur in LiDAR and Radar components such as assembly at the vehicle factory and shipping of the dealer.
It is necessary to calibrate such an installation offsets at the factory or dealer so that it does not affect the irradiation position of LiDAR or Radar or the position accuracy of the detected object in the 3D map.
Therefore, in factories and dealers, tilt detection is performed with a 3-axis accelerometer in a stand-still environment to measure installation offsets, and when driving → vehicle stop, data from the 3-axis gyroscope is also used to measure the tilt of LiDAR and Radar components.
A 6in1 sensor, which is a 6-axis combo sensor that combines 3-axis acceleration sensor and 3-axis gyro sensor (angular velocity sensor) into a single chip, can achieve both of these functions.
[What's good in 6in1?]
- When the temperature is constant and the vehicle is stand-still, the acceleration sensor can detect a tilt of 0.2°.
- 0.1° can be detected by using gyroscope (angular rate sensor) data in an environment where the temperature is constant and there is some movement.
2 : Achieves stable sensing with accurate object position /ego-vehicle position even in harsh environments
"In case of the sensor as LiDAR that has a long scanning cycle, it is necessary for system to compare the point cloud of the surrounding environment detected in the previous cycle with the point cloud detected in the current cycle.
By using the vehicle motion data from the 6-axis sensor, it is possible to reduce the amount of calculation for matching the point cloud in the previous cycle and the one in the current cycle.
When driving, the 6in1 sensor can dynamically detect swells on hills and roads, and based on the sensor data, the system can correct the laser irradiation position or the position of the detected object on the map.
Furthermore, even if the GNSS is interrupted in a tunnel, the system can calculate the altitude and azimuth by detecting the slope and the traveling direction of the vehicle, and can estimate the vehicle position in the detected 3D map and 2D navi-map.
[What's good in 6in1?]
- With 8kHz high data output rate, the system can enable vehicle motion detection during the scanning cycle and continuously assist in recognizing the position of the detected object and own vehicle position.
- Even in systems such as LiDAR/Radar that are exposed to high temperature and high vibration environments, stable detection data can be transmitted to the system.
3 : Achieves both 6-axis detection and functional safety
LiDAR and Radar play an important role in safety, and the system is often required to comply with functional safety (ISO26262).At the system level, ASIL-D is often required. Functional safety requirements have begun for devices such as inertial sensors installed in LiDAR/Radar system.
Panasonic's 6in1 sensor is equipped with a diagnostic function for all 6 axes mounted in 1-chip MEMS, and the sensor chip complies with ASIL-B(D). Therefore, by mounting one 6in1 sensor, it is possible to achieve both 6-axis detection and functional safety in a system that requires 6-axis inertial sensor and functional safety compliance without mounting multiple inertial sensors.
[What's good in 6in1?]
-
By mounting a 6in1 sensor that is compatible with ASIL-B(D) and 6-axis detection, both 6-axis detection and functional safety compliance can be achieved with one chip.
In addition, it is possible to comply with functional safety with a single chip, eliminating the need to mount multiple sensors and reducing the BOM cost more than before.