Automotive Trend into the “CASE” Era and Technology Issues (1)
- 48-V System Mild Hybrid -
2019-11-18
- Attention-getting Mild Hybrid in Tightening Exhaust Gas Regulations
- Efficiency Improvement by 48-V Mild Hybrid Vehicles
- Mild Hybrid Operation during Acceleration and Deceleration of Vehicles
- Bidirectional DC/DC Converter Connecting 12-V and 48-V Systems
- Related product information
- Tags related to this article
The word "CASE" (Connected、Autonomous、Shared & Services、Electric) is being used more often as a new style of automobile or mobility. In such a trend, unprecedented technologies and concepts are being proposed, and a variety of engineering issues are also emerging at the same time. In this column, from the engineering trend around automobiles, we will explore several themes related to electronics.
Attention-getting Mild Hybrid in Tightening Exhaust Gas Regulations
In an effort to suppress global warming, which is thought to be one of the causes of large-scale climate change, a variety of actions have been taken to reduce CO2 exhaust by automobiles. In the EU, where particularly strict exhaust gas regulations are enforced, and in anticipation of additional regulations in the future, conformance to the regulations forces a greater development burden on the automobile manufacturers.
In such an environment, an attention-getting drive system for reducing CO2 exhaust by utilizing the basic design of existing gasoline or diesel vehicles is the “Mild Hybrid” system.
A mild hybrid vehicle is equipped with a small capacity secondary battery and auxiliary motor, with startup and acceleration being assisted by the motor. This mechanism can lower fuel consumption of the engine, and by combining this with an idling stop function, a fuel consumption reduction of about 20% is said to be achieved.
Hybrid vehicles (HEV) and plug-in hybrid vehicles are called “strong hybrid vehicles” and are superior to mild hybrid vehicles in fuel economy, but their structures are complex and require many man-hours to develop.
Because a mild hybrid vehicle can be developed on the base of an existing chassis and power train, many auto manufacturers, primarily German manufacturers, are trying to meet the exhaust gas regulations using mild hybrid vehicles instead of strong hybrid vehicles. Some auto-manufacturers in Japan are also actively working on mild hybrid vehicles.
Efficiency Improvement by 48-V Mild Hybrid Vehicles
A brief configuration of a mild hybrid vehicle is shown in Fig. 1.
Large differences in structure from a normal vehicle is as shown below.
- Newly added 48-V electrical system
- A 48-V system consists of a motor (alternator during deceleration) for assisting the engine during acceleration, a secondary battery for supplying current to the motor, and other equipment.
- The 48-V system and 12-V system are connected by a bidirectional DC/DC converter.
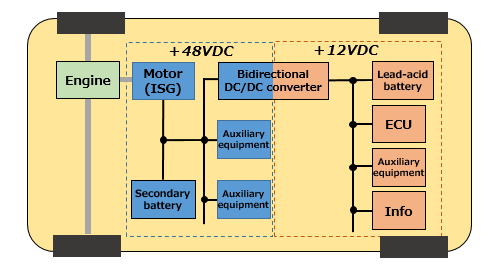
48-V system | 12-V system |
---|---|
Motor (integrated function of a motor and alternator)
Secondary battery Power steering unit Air conditioner Cooling fan |
Lead-acid battery
Engine control Transmission control Brake control ADAS Infotainment (car navigation system, etc.) |
One of the new points is the newly added 48-V system.
For automobiles, except in large vehicles, a 12-V output lead-acid batteries have been used traditionally.
However, in a mild hybrid system, both the power to drive the motor during acceleration and the power recovered using the motor as a generator during deceleration are large, which would cause the current value to reach several hundred amperes if a 12-V system is used.
In addition, conventional 12-V systems are not suitable for mild hybrids in the first place, because lead-acid batteries should not be charged and discharged rapidly. In addition, some supporting equipment, such as power steering, has already been reaching limits with a 12-V system, and higher voltage supply is required.
As a result, separate from the 12-V system, a new voltage system suited for operating a mild hybrid was proposed - a 48-V system.
By raising the voltage 4 times, the current for supplying the same power can be reduced to 1/4, making the power loss in the harness smaller, without requiring a thick and heavy harness. When we look at voltage, 48 V is not so high, and circuit construction is easier even when including safety measures.
Mild hybrid and 48-V systems are not the same thing, but are based on a similar background, using 12 V and 48 V in conjunction is becoming popular. Naturally, a mild hybrid consisting of a voltage other than 48 V does exist.
Mild Hybrid Operation during Acceleration and Deceleration of Vehicles
A brief operation of mild hybrids during acceleration and deceleration is shown below.
- During acceleration
Driving the motor using secondary battery power assists acceleration, thereby reducing the fuel consumption of the engine and improves fuel economy. (Fig. 2)Fig. 2. Operation example of mild hybrid vehicle during acceleration - During deceleration
A motor is used as an alternator to store energy in the secondary battery. At the same time, the lead-acid battery in the 12-V system is also charged. This is called regenerative braking. (Fig. 3)Fig. 3. Operation example of mild hybrid vehicle during deceleration
The motor for the mild hybrid not only assists acceleration but also works as an generator (alternator) during deceleration. This motor often assumes the starter motor function, and the unit is called ISG (Integrated Starter Generator).
The secondary battery assumes the role of storing power generated by the motor during deceleration in a short time, and the role of instantly supplying power required by the motor during acceleration. Because the 12-V output lead-acid battery loaded on the car cannot be used for rapid charging/discharging, a lithium-ion battery with excellent performance is mainly used in a mild hybrid system. Naturally, it does not require as much capacity as the strong hybrid.
Bidirectional DC/DC Converter Connecting 12-V and 48-V Systems
When looking at this system from the viewpoint of electronics, the unique structural element for mild hybrids is the bidirectional DC/DC converter. This converter assumes the role of connecting the existing 12-V system and a new 48-V system consisting of a motor, secondary battery, and auxiliary equipment.
<12 V→48 V voltage increasing motion >
When driving 48-V auxiliary equipment from the 12-V lead-acid battery, or the charged level of the secondary battery is insufficient for assisting operations, the secondary battery is charged from the 12-V lead-acid battery by using a voltage-raising operation.
<48 V→12 V voltage reduction motion>
Voltage reduction motion is used for charging the 12-V lead-acid battery by using the regenerated power of the 48-V motor (alternator).
Shown in Fig. 4 is a structure example of the simplest bidirectional DC/DC converter by combining a voltage reduction chopper circuit and voltage raising chopper circuit.
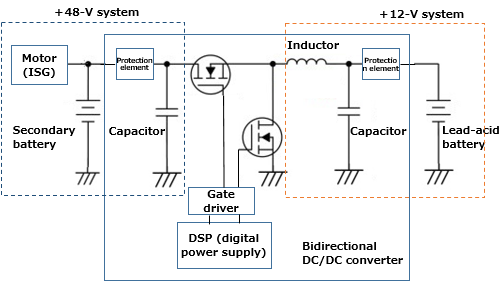
The switching power supply (DC/DC converter) loaded on the in-vehicle ECU can be structured, in principle, by using commercially available switching power ICs as explained in “Basic Knowledge of Power Supply Circuit (3) - Switching regulator design procedure” or “Basic Knowledge of Power Supply Circuit (4) - “Design key-point of power supply circuit for ECU.”
On the other hand, the bidirectional DC/DC converter of the mild hybrid needs to finely control the voltage increase function from the 12-V system to 48-V system while monitoring the condition of the 12-V and 48-V systems, and the voltage decreasing function from the 48-V system to 12-V system. The power capacity has a large range from a couple of kW to 10 kW or more, so unless high efficiency is achieved, heat generation (loss) may become a problem from handling such a large capacity. Due to these reasons, controlling switching operations by using a digital circuit such as DSP (Digital Signal Processor), so-called digital power supply implementation, is becoming the mainstream.
When designing a bidirectional DC/DC converter for 12-V and 48-V, and supporting equipment connected to 48-V systems, special caution is required for the rated voltages of electronic components. According to the LV 148 standard, the voltage range of the 48-V system is specified as 36 V to 52 V, and the over-voltage limit is limited to 60 V, so, selecting electronic components rated at 60 V or higher throughout the estimated operating temperature range would be desirable.
In the next article, we’ll pick up batteries installed in EVs, etc., and peripheral circuits.