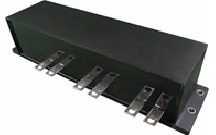
Stricter environmental regulations, such as CO2 reduction, enforced in various countries have led to a sharp growth in the eco-friendly vehicle (xEV) market. Seeing the growing xEV market, car manufacturers today are keen on expanding their lineup of xEV vehicles. To expand the xEV lineup, they have to replace gas-powered vehicles with xEV vehicles, which need important parts—DC-link capacitors for driving inverters. Now, there is a strong demand for small high-performance film capacitors to be used as DC-link capacitors.
Panasonic has met this demand for the smallness and high performance of its capacitor through its high-precision vapor deposition technology and provided the capacitor's film with a fuse structure, making the capacitor an extremely safe product. With these achievements, Panasonic has been a leading player in hybrid vehicle development since its early stage and still keeps its top-class share in the hybrid vehicle market among rivals in the industry.
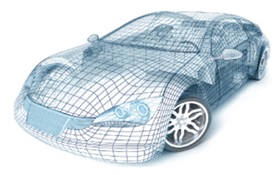
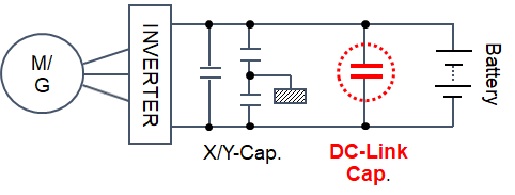
Product features
- High safety
Miniaturization - High power output
-
High safety: This capacitor is provided with a security mechanism (fuse), which ensures the safety of the product (open failure mode).
The product's original security mechanism (high-precision pattern deposition), in which fuses are arranged in an optimum pattern on a deposited film, leads any failure mode to an open failure mode, thus preventing ignition/smoking accidents caused by a short failure mode, thus contributing to the high safety of vehicles.
Fuse function Safety limits DC step-up test Example of security test results
Start from the rated voltage (W.V.) and increase the applied voltage by 50 V every 10 minutes
Ambient temperature 110°CFuse Function Technology of Panasonic Film Capacitors | Panasonic
In this video, we’ll review the Fuse function Technology that is built into Panasonic Film Capacitors.
-
Miniaturization: To achieve miniaturization of the capacitor, a highly voltage-resistant PP film with reduced thickness was adopted as the capacitor's film to lessen the capacitor's thickness.
With help from film manufacturers, Panasonic has developed the highly voltage-resistant film with reduced thickness and used it as the capacitor's film to lessen the capacitor in thickness. Panasonic has thus achieved the miniaturization of the capacitor, paving the way to reduce the inverter in size and weight.
-
High power output: Panasonic's original vapor deposition technology alleviates self-heating by the capacitor (lowers the ESR of the capacitor), allowing the capacitor to handle the high power output of the inverter.
The high current pattern deposition (patented technology) and high current heavy edge construction method, which are Panasonic's original technologies, alleviate self-heating (lower ESR) to allow the capacitor to carry a larger allowable current, thus contributing to an increase in power output from the inverter.
- 1)High current pattern deposition
(patented technology) - Generally, a pattern formed on a deposited film increases the ESR of the film, and consequently, the film shows a sharper self-temperature rise caused by a ripple current. However, Panasonic has changed this pattern into a special pattern that minimizes the ESR value, thus succeeding in keeping the self-temperature rise at a low level.
Comparison of self-temperature rise curves caused
by ripple current- 2)High current heavy edge construction method
- A part where a deposited film and a metallic surface coating (outer electrode) are in contact with each other tends to be an unstable connecting part, where ESR irregularities arise due to contact resistance.
However, Panasonic has solved this problem by adopting the heavy edge construction method by which the part of deposit film that is in contact with the metallic surface coating is increased in thickness. This makes the connecting part stable and reduces the ESR irregularities.
The method also suppresses deterioration in contact (increase in ESR) when the pulse current is applied to the contact part.
Element structure Pulse current step-up test (image) - 1)High current pattern deposition
Extra benefits to customers
-
Quick product development by highly accurate design simulations
Panasonic's database containing accumulated data from 20 years of business experience allows accurate simulations of current-caused self-heating and ESL values. This allows the company to meet a customer's request for custom design and complete the target design in a short period, thus leading to faster development of new vehicles.
- Example) Simulation of current-caused heat generation
-
・Simulation values ⇒ input necessary data
(structure, current, ESR, temperature, etc.) and calculate the simulation values. - ・Actual measurements ⇒ attach thermocouples to various parts and take measurements
- Simulation values roughly match actual measurements (maximums)
-
- Product characteristics can be predicted in the design review stage.
-
Design and production systems established by numerous production sites worldwide achieved global support and stable delivery to customers.
These design and production systems are at work in Japan, China, and Europe, where the systems provide quick support for and stable delivery to customers.
- ● Advantages the global network of many production sites offers
- 1)Design-related support provided in local languages as local customer service allows smooth product marketing.
- 2)Production in locations close to customers allows a reduction in delivery lead times.
- 3)The global production site network is advantageous from the viewpoint of a business continuity plan (BCP). If a production site fails to deliver a product, another production site can provide backup and deliver the product.
- 4)All production sites run the same automatic production equipment. Therefore, when the number of product orders increases, multiple production sites can manufacture products of the same quality and deliver them to customers.
Region Europe China Japan Design sites Lüneburg, Germany Shanghai Tonami City, Toyama Prefecture Production sites Slovakia Jiangmen City Tonami City, Toyama Prefecture Toyama / Matsue Factory Names of production sites Panasonic Industrial Devices Slovakia s.r.o
(PIDEU-SK)Panasonic Electronic Devices(Jiangmen) Co.,Ltd
(PEDJM)Toyama / Matsue Factory
(Toyama site)Toyama / Matsue Factory
(Matsue site)