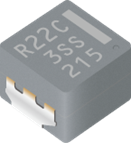
Developped a 7 mm square automotive power inductor with a low inductance of 0.22 μH designed for ECU (Electronic Control Unit) applications used in ADAS (Advanced Driver Assistance Systems) and autonomous driving systems. The inductor has adopted a high permeability metal composite material composed of the company's proprietary material to achieve lower DC resistance of 0.71 mΩ.
What is 7 mm Square Automotive Power Inductor with Low Inductance?
Three features of 7 mm Square Automotive Power Inductor with Low Inductance
The size and weight of ECU housings can be reduced, thereby contributing to a reduction in environmental impact.
The product has achieved lower DC resistance of 0.71 mΩ as a low inductance inductor (0.22 μH) with a size of 7 mm square, through the adoption of a high permeability metal composite material composed of the company's proprietary material.
Focusing on the metal composite material for sealing the internal coil, Panasonic Industry has improved the permeability through the company's proprietary material composition, and achieved lower DC resistance of 0.71 mΩ for this product with the specifications of a 7 mm square size and inductance of 0.22 μH.
Reduces the stress generated in the bending section of the product terminals caused by driving or vibrations from the engine by approximately 65% compared to the company's conventional product (compliant with the AEC-Q200 reliability test standard for certification of automotive passive components)
When vibrations are applied to an inductor from the outside, the breakage of the terminals leads to a product defect. This product is designed to pull out the lead wires from the center position and shorten the length of the terminals, thereby reducing stress by approximately 65% and further improving vibration resistance.
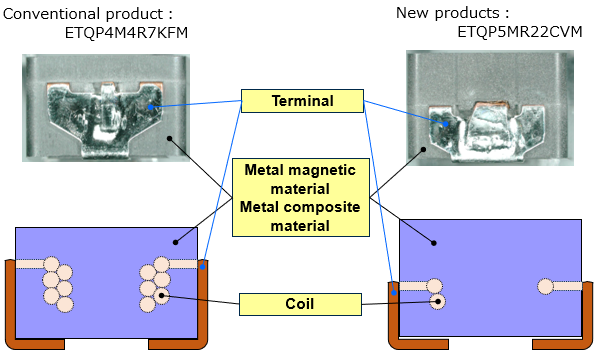
Its capability to pass large currents (rated current of 32.0 A) contributes to the reduction of the number of power lines. The size and weight of ECU housings can be reduced, thereby contributing to a reduction in environmental impact.
Since this product can pass large currents (rated current of 32.0 A), it is possible to reduce the number of power lines by increasing the current that can flow through each power line on the ECU circuit board. This enables the reduction of the circuit board area and materials when this product is mounted, which also contributes to the reduction of the environmental impact.
<Image of reducing the number of power lines>
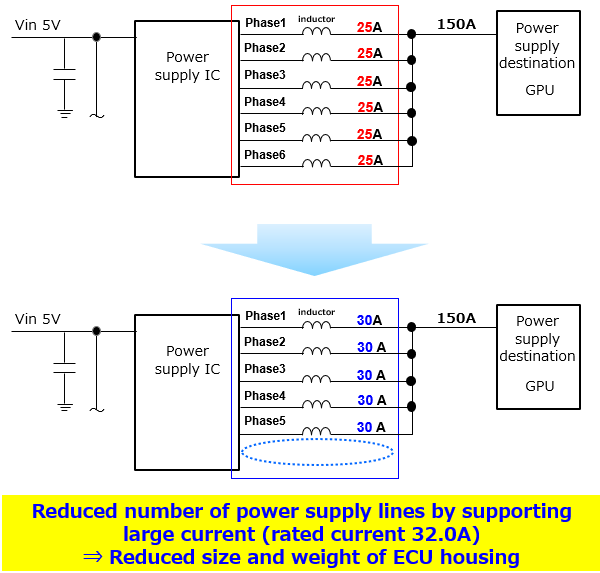
Use example
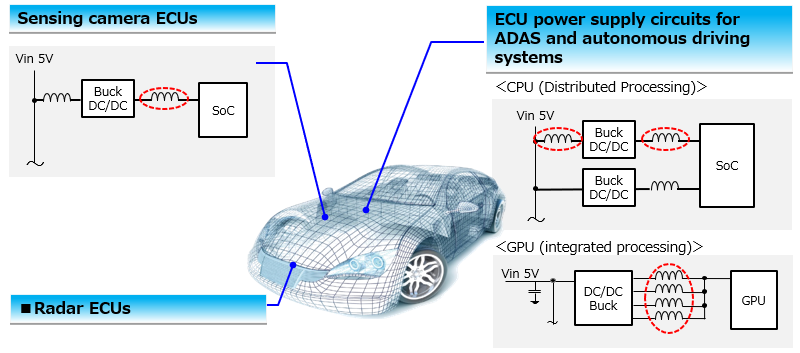
Lineup
Product number | Shape W×D×H (mm) |
Inductance (*1) (µH) |
DC resistance 20°C (mΩ Typ) |
Rated current (*2) (A) |
---|---|---|---|---|
ETQP5MR22CVM | 7.6 × 7.0 × 5.0 | 0.22 | 0.71 | 32.0A |
(*2): Current value that causes a temperature rise of 40°C