What Is EPS?
- System that assists driver in operating the steering wheel with power from motor -
2023-12-22
An EPS is a system that assists the driver in operating the steering wheel with power from a motor, allowing the driver to use less force to turn the steering wheel. Adopting the EPS improves the mileage of the vehicle and may reduce the overall weight of the vehicle as well. This article will discuss the functions and system configuration of the EPS and will introduce the electronic components making up the EPS as well.
What is EPS?
Brief description of the EPS
Electric power steering (EPS) is a type of power steering system that assists the driver in operating the steering wheel with power from a motor. The conventional hydraulic power steering system assists the driver in steering operation by actuating a hydraulic pump using power from the engine. The EPS, on the other hand, assists the driver through electric control based on steering operation information. The EPS does not consume engine power that the hydraulic power steering needs, and is therefore expected to improve the mileage.
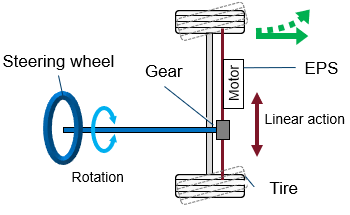
Technological shifts in the power steering system
- Electrification
The system is driven by power from the battery, which leads to better mileage and simplified mechanisms. In autonomous driving mode, the vehicle is required to take overall control of the vehicle’s behavior. To make this happen, electrification of in-vehicle equipment is essential. - By-wire connection
The steering wheel shaft and the axle are mechanically separated from each other and are electrically connected, instead. Mechanical separation of such components allows more precise operations/controls. At a higher autonomous driving level, the vehicle itself is mainly responsible for steering operations as the driver’s role becomes less important to make it less necessary for the driver to grab the steering wheel. It is assumed that in the most advanced form of autonomous driving, steering is no longer needed as the axle and wheels are automatically controlled.
Fig. 2 Configuration change resulting from by-wire connection - Redundant structure
For improved safety and reliability, a motor-driving inverter, etc., is given a redundant structure composed of two inverters.
Fig. 3 Configuration changes resulting from the adoption of a redundant structure
Trends in the market and demand for the EPS
The number of EPSs incorporated in vehicles is expected to increase. Currently, most autonomous driving vehicles produced have a level 2 or lower lever of autonomous driving function. It is assumed, however, that an improvement in the autonomous driving level will increase by-wire connections. By-wire connections replace mechanical connections and need more motors. In general, to improve the safety and reliability of the EPS, double-structured (redundantly structured) motor control circuits are incorporated in the EPS, and this raises a concern about increasing power consumption. To solve these problems, electronic components making up the EPS are required to have these properties: "low loss," "high resistance to heat," "high precision (temperature)," and "small size."
Circuit configuration of the EPS
Overall configuration
- Noise filter: Suppresses internal noise or noise from external equipment
- Voltage conversion circuit: Converts voltage by switching of FETs, etc. It also measures the temperatures of them.
- Gate drive circuit: Controls the gates of the switching elements
- Control circuit: Controls the circuit as a whole
- DC/DC converter: Supplies power to the control circuit
- Communication I/F: A communication circuit that communicates with external equipment
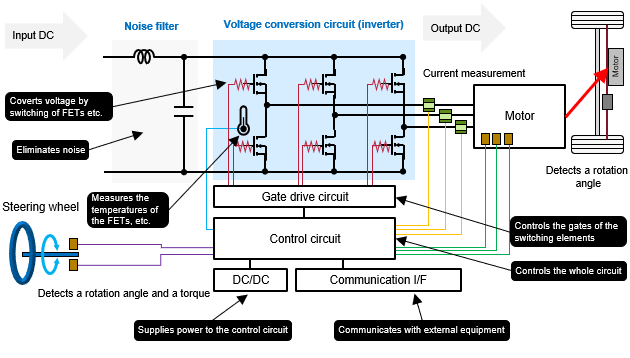
Individual circuits and components
Noise filter
The noise filter suppresses internal noise or noise from external equipment, thereby preventing malfunctioning of the system. In general, the filter combines a large coil and a capacitor together.
Noise elimination and smoothing: Conductive polymer hybrid aluminum electrolytic capacitor
POINT- ❶ The capacitor offers high capacitance, low ESR, and high ripple-suppression performance, thus contributing to a reduction in the size of the circuit and an increase in the power capacity (low voltage and large current) of the circuit.
- ❷ Having capacitance characteristics to cut off high-frequency components, the capacitor eliminates a wide range of high-frequency noises that are generated by the high-frequency switching of the circuit.
Voltage conversion: Power Inductors for Automotive application
POINT- ❶ The inductor made of a metal magnetic material suffers less power loss and carries a large current, thus contributing to a reduction in the size of the circuit and an increase in the power capacity (low voltage and large current) of the circuit.
- ❷ Having loss characteristics in a higher frequency range (low ACR), the inductor contributes to the suppression of power loss caused by high-frequency switching of the circuit.
Voltage conversion circuit
The voltage conversion circuit converts voltage by switching elements. The switching elements switch on and off to make voltage conversion, but these switching actions create noise. To suppress this noise, gate terminals of these switching elements (FETs) are made up of resistors. High-power operations cause the switching elements, etc., to heat up. To prevent a failure of such elements whose temperature may rise above the upper limit temperature, generally, the temperature of these elements is measured with an NTC thermistor.
Suppressing gate-driving noise by the switching elements, electric discharge by the film capacitor: Chip resistor (small and high-power chip resistor)
POINT- ❶ With its original resistance pattern, electrode structure, etc., the chip resistor is small in size and yet handles high-power operations, thus contributing to a reduction in the size of the circuit.
Measuring the temperature of the switching elements, etc.: NTC thermistor (chip-type)
POINT- ❶ The thermistor is small, highly resistant to heat, and original external electrode forming technology that offers high reliability, thus contributing to highly precise temperature compensation in the circuit.
DC/DC converter
The DC/DC converter is composed mainly of an FET, a coil, and capacitors. In the DC/DC converter generally, a conductive polymer hybrid aluminum electrolytic capacitor is used to eliminate noise to the input end and to smooth voltage output from the output end, and an in-vehicle power inductor is used for voltage conversion.
Noise elimination, switching, and smoothing: Conductive polymer hybrid aluminum electrolytic capacitor
POINT- ❶ The capacitor offers high capacitance, low ESR, and high ripple-suppression performance, thus contributing to a reduction in the size of the circuit and an increase in the power capacity (low voltage and large current) of the circuit.
- ❷ Having capacitance characteristics to cut off high-frequency components, the capacitor eliminates a wide range of high-frequency noises that are generated by the high-frequency switching of the circuit.
Noise elimination and smoothing: Power Inductors for Automotive application
POINT- ❶ The inductor made of a metal magnetic material suffers less power loss and carries a large current, thus contributing to a reduction in the size of the circuit and an increase in the power capacity (low voltage and large current) of the circuit.
- ❷ Having loss characteristics in a higher frequency range (low ACR), the inductor contributes to the suppression of power loss caused by high-frequency switching of the circuit.
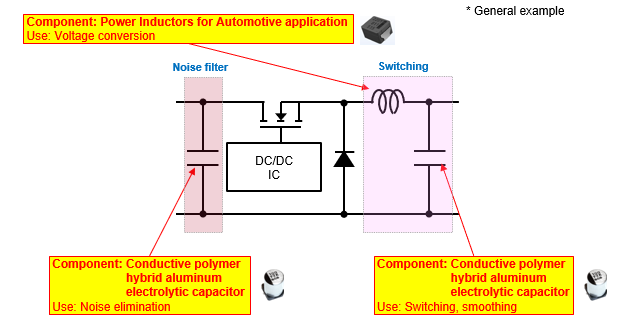
Communication I/F
The communication I/F circuit communicates with external equipment (CAN, Ethernet, etc.) through two communication lines. If noise or static electricity enters these communication lines, it may cause a transceiver IC to fail. To prevent such a problem, the transceiver circuit is usually provided with chip varistors serving as electrostatic control measures.
ESD noise elimination: Chip varistor
POINT- ❶ With a wide range of capacitance characteristics, the chip varistor suppresses electrostatic discharge (ESD) noise while keeping the communication quality of the circuit intact.
- ❷ With its capacitance ranging from 8 pF to 250 pF, the chip varistor operates effectively at low to high communication speeds.
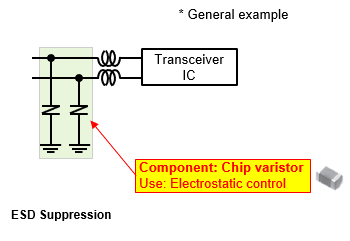
Summary
The EPS is the system that assists the driver in operating the steering wheel with power from the motor. It is assumed that improvement in the autonomous driving level will increase by-wire connections totally depending on electric control. Consequently, the number of EPSs incorporated in vehicles is expected to increase as well. By-wire connections replace mechanical connections making up the hydraulic power steering system, etc., but need more motors. Increased motors consume more power, leading to increasing power consumption by the vehicle. In addition, the higher autonomous driving level requires further improvement in system safety and reliability, which promotes the tendency to give motor control circuits a redundant structure. To keep pace with such technological advancement, the electronic components making up the EPS are required to have these essential properties: "low loss," "high resistance to heat," "high precision (temperature)," and "small size." Panasonic Industry offers a wide variety of products for use in the EPS (Table 1).
Component | Feature | Low loss | Small size | High resistance to heat | High precision |
---|---|---|---|---|---|
Conductive polymer hybrid aluminum electrolytic capacitor![]() |
Low ESR High reliability |
✔ | ✔ | ✔ | |
Power Inductors for Automotive application ![]() |
Large current, low loss High reliability |
✔ | ✔ | ✔ | |
![]() |
High precision, high resistance to heat | ✔ | ✔ | ||
Chip varistor![]() |
Small and light | ✔ | |||
NTC thermistor (chip-type)![]() |
Small, high resistance to heat | ✔ | ✔ | ✔ |