AEC-Q200
What is AEC-Q200 (passive component reliability test standard)?
2023-09-29
An automobile carries an electronic control unit (ECU) composed of numerous electronic components. These electronic components must operate normally even when the automobile runs in a harsh environment. Different from electronic components making up consumer products, in-vehicle electronic components are required to meet more severe quality requirements.
AEC standards provide quality management requirements that in-vehicle semiconductor devices should meet. Among various types of standards included in the AEC standards is AEC-Q200 which focuses on passive components. This article will discuss AEC-Q200 and brief on Panasonic products conforming to AEC-Q200 as well.
AEC-Q200 included in AEC standards
What are AEC standards?
Automotive Electronics Council or AEC was set up in the 1990s by three leading automobile manufacturers in the United States and joined by major electronic component manufacturers. The organization is responsible for setting common standards for in-vehicle electronic components including quality standards. Its AEC Component Technical Committee is working on setting standards for reliable electronic components and component certification rules.
AEC standards are international standards for ensuring the reliability of in-vehicle electronic components. Automobile manufacturers will not purchase components that fail to meet the requirements defined in the standards. AEC standards provide various types of standards applied to different types of electronic components. Among them is AEC-Q200 which applies to passive components. Passive components refer to components that consume, store, or release supplied power.
- AEC-Q100: integrated circuits (IC)
- AEC-Q101: discrete semiconductor products (capacitors, transistors, diodes, etc.)
- AEC-Q102: discrete optoelectronics semiconductor products (LEDs, etc.)
- AEC-Q103: vehicular sensors
- AEC-Q104: multichip modules (containing multiple chip pairs, ICs, etc.)
- AEC-Q200: passive components (resistors, capacitors, inductors, etc.)
AEC-Q200 grades
AEC standards classify components into different grades corresponding to their service temperature ranges. These grades define individual places where classified components are allowed to be used. AEC-Q200 provides five grade categories, and components with a lower grade number must be able to withstand lower and higher temperatures.
Table 1 Guaranteed temperature range and applicable locations for each grade
Grade | Temperature range | Typical places of use of components | |
---|---|---|---|
Low temperature |
High temperature |
||
0 | -50°C | +150°C | Every mounting part |
1 | -40°C | +125°C | Most of the engine room |
2 | -40°C | +105°C | High-temperature area of the passenger room |
3 | -40°C | +85°C | Most of the passenger room |
4 | 0°C | +70°C | A place for mounting non-electrical equipment |
AEC-Q200 test items
To run safely in a harsh environment, an automobile must have its electronic components keep operating normally. These electronic components cannot be put on the market as components conforming to AEC-Q200 requirements unless they pass environment tests, electrical tests, etc., conducted under severe test conditions. Passive components to be certified by AEC-Q200 tests and test items to be applied are listed in the following table.
Various components to be tested include capacitors, resistors, varistors, and crystal vibrators, with test items being specified for each component. Test items vary also depending on whether a component to be tested is a lead component or a surface mount device (SMD). In addition, capacitors of different types should be tested with different test items. So, these tests must be conducted carefully.
Test No. |
Stress・Test | Components | |||||||||||||||
---|---|---|---|---|---|---|---|---|---|---|---|---|---|---|---|---|---|
Tantalum and Niobium Capacitors | Ceramic Capacitors | Aluminum Electrolytic Capacitor | Film Capacitor | Magnetics | Networks | Resistors | Thermistors | Trimmer Capacitors/ Resistors | Varistors | Quartz Crystals | Ceramic Resonators | EMI Suppressors / Filters | Polymeric Resettable Fuses | Fuses | Super Capacitor | ||
Table No. | |||||||||||||||||
1 | 2 | 3 | 4 | 5 | 6 | 7 | 8 | 9 | 10 | 11 | 12 | 13 | 14 | 15 | 16 | ||
1 | Pre- and Post- Stress Electrical Test | ✕ | ✕ | ✕ | ✕ | ✕ | ✕ | ✕ | ✕ | ✕ | ✕ | ✕ | ✕ | ✕ | ✕ | ✕ | ✕ |
3 | High Temperature Exposure (Storage) | ✕ | ✕ | ✕ | ✕ | ✕ | ✕ | ✕ | ✕ | ✕ | ✕ | ✕ | ✕ | ✕ | ✕ | ||
4 | Temperature Cycling | ✕ | ✕ | ✕ | ✕ | ✕ | ✕ | ✕ | ✕ | ✕ | ✕ | ✕ | ✕ | ✕ | ✕ | ✕ | ✕ |
5 | Destructive Physical Analysis | ✕ | ✕ | ||||||||||||||
7 | Humidity Bias | ✕ | ✕ | ✕ | ✕ | ✕ | ✕ | ✕ | ✕ | ✕ | ✕ | ✕ | ✕ | ✕ | ✕ | ✕ | ✕ |
8 | High Temperature Operating Life | ✕ | ✕ | ✕ | ✕ | ✕ | ✕ | ✕ | ✕ | ✕ | ✕ | ✕ | ✕ | ✕ | ✕ | ✕ | ✕ |
9 | External Visual | ✕ | ✕ | ✕ | ✕ | ✕ | ✕ | ✕ | ✕ | ✕ | ✕ | ✕ | ✕ | ✕ | ✕ | ✕ | ✕ |
10 | Physical Dimensions | ✕ | ✕ | ✕ | ✕ | ✕ | ✕ | ✕ | ✕ | ✕ | ✕ | ✕ | ✕ | ✕ | ✕ | ✕ | ✕ |
11 | Terminal Strength (Leaded) | ✕ | ✕ | ✕ | ✕ | ✕ | ✕ | ✕ | ✕ | ✕ | ✕ | ✕ | ✕ | ✕ | ✕ | ✕ | ✕ |
12 | Resistance to Solvent | ✕ | ✕ | ✕ | ✕ | ✕ | ✕ | ✕ | ✕ | ✕ | ✕ | ✕ | ✕ | ✕ | ✕ | ✕ | ✕ |
13 | Mechanical Shock | ✕ | ✕ | ✕ | ✕ | ✕ | ✕ | ✕ | ✕ | ✕ | ✕ | ✕ | ✕ | ✕ | ✕ | ✕ | ✕ |
14 | Vibration | ✕ | ✕ | ✕ | ✕ | ✕ | ✕ | ✕ | ✕ | ✕ | ✕ | ✕ | ✕ | ✕ | ✕ | ✕ | ✕ |
15 | Resistance to Soldering Heat | ✕ | ✕ | ✕ | ✕ | ✕ | ✕ | ✕ | ✕ | ✕ | ✕ | ✕ | ✕ | ✕ | ✕ | ✕ | |
17 | ESD | ✕ | ✕ | ✕ | ✕ | ✕ | ✕ | ✕ | ✕ | ✕ | ✕ | ||||||
18 | Solderability | ✕ | ✕ | ✕ | ✕ | ✕ | ✕ | ✕ | ✕ | ✕ | ✕ | ✕ | ✕ | ✕ | ✕ | ✕ | ✕ |
19 | Electrical Characterization | ✕ | ✕ | ✕ | ✕ | ✕ | ✕ | ✕ | ✕ | ✕ | ✕ | ✕ | ✕ | ✕ | ✕ | ✕ | ✕ |
20 | Flammability | ✕ | ✕ | ✕ | ✕ | ✕ | ✕ | ✕ | ✕ | ✕ | ✕ | ✕ | ✕ | ✕ | |||
21 | Board Flex | ✕ | ✕ | ✕ | ✕ | ✕ | ✕ | ✕ | ✕ | ✕ | ✕ | ✕ | ✕ | ✕ | ✕ | ✕ | |
22 | Terminal Strength (SMD) | ✕ | ✕ | ✕ | ✕ | ✕ | ✕ | ✕ | ✕ | ✕ | ✕ | ✕ | ✕ | ✕ | ✕ | ✕ | ✕ |
24 | Flame Retardance | ✕ | |||||||||||||||
25 | Rotational Life | ✕ | |||||||||||||||
27 | Surge Voltage | ✕ | |||||||||||||||
30 | Electrical Transient Conduction | ✕ | ✕ | ||||||||||||||
32 | Short Circuit Fault Current Durability | ✕ | |||||||||||||||
33 | Fault Current Durability | ✕ | |||||||||||||||
34 | End-of-Life Mode Verification | ✕ | |||||||||||||||
35 | Jump Start Endurance | ✕ | |||||||||||||||
36 | Load Dump Endurance | ✕ |
Conclusion
AEC standards are international standards for ensuring the reliability of in-vehicle electronic components. AEC-Q200, which is included in the AEC standards, is the standard applied to passive components. These components must pass tests conducted under severe test conditions first before they are put on the market as products conforming to AEC-Q200. Panasonic offers a lot of components conforming to AEC-Q200, thus contributing to the development of in-vehicle products.
Related product information
Tags related to this article
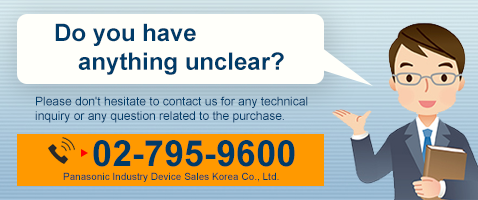