What Is ESC?
- Technology for Preventing the Skid of a Vehicle to Improve Driving Safety -
2024-3-22
Electronic Stability Control (ESC) is a technology for improving the steering stability of a car. The ESC prevents wheels from skidding off (locked wheels side-slipping over the road surface) and assists the driver in driving the car in the intended direction. This function of ESC improves stability of the car while traveling around a curve or on a slippery road, thus reducing the risk of a traffic accident. This article discusses the functions and system configuration of ESC and introduces the electronic components making up the ESC as well.
What Is ESC?
Outline of ESC
ESC is a combination of these three technologies: anti-lock braking system (ABS), traction control system (TCS), and yaw control. ESC combines together a position stabilizing function, an anti-slip function, and a braking assist function, thus offering improved stability of the vehicle. Specifically, it controls each of the brakes, attached to the four wheels, based on various pieces of sensing information, thereby performing meticulous position control. The system is particularly effective in reducing the risk of a traffic accident under slippery road conditions or situations where emergency evasive action is required.
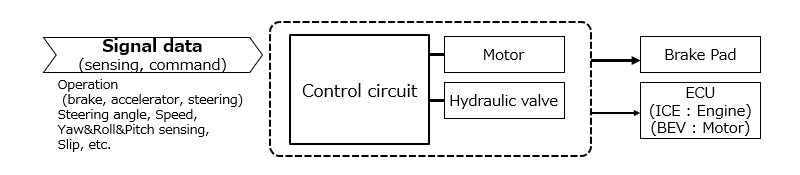
Difference between ABS and ESC
ABS and ESC look similar, but are different in essence. The main function of ABS is to prevent wheels from locking when the driver hits the brake hard. ABS allows the driver to keep the vehicle in control during braking and alleviates skidding behavior of the vehicle, but is unable to control sideslip of the vehicle.
ESC, on the other hand, prevents slip or skid of the vehicle, allowing the driver to exert total control over the vehicle. This function of ESC improves the stability of the vehicle around curves or when it drives on irregular road surfaces. Different from the ABS, ESC is capable of controlling sideslip of the vehicle.
System | Control details | Effect |
---|---|---|
ABS | Each of the brakes attached to the four wheels works under the same pressure. The brake is controlled intermittently so as not to lock the tire. |
A vehicle equipped with ABS has a shorter braking distance than a vehicle not equipped with ABS. ABS cannot control sideslip of the vehicle. |
ESC | Each of the brakes attached to the four wheels works under a different pressure. The brake is controlled intermittently so as not to lock the tire. The pressure for each brake is changed so as to curb sideslip of the vehicle. |
A vehicle equipped with ESC has a shorter braking distance than a vehicle not equipped with ESC. ESC can control sideslip of the vehicle. |
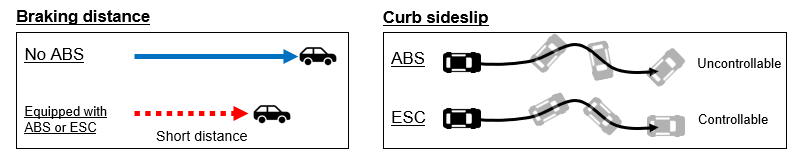
Trends in the Market and Demand for ESC
Many vehicles are already equipped with ABS or ESC, with the number of these systems expected to increase as the number of vehicles carrying the systems increases. Equipment making up these systems needs further improvement, to meet the requirement in achieving the high accuracy in brake control, for the traveling performance of the vehicle. In addition, there also are demands for miniaturization of equipment to allow for longer mileage and system redundancy in ensuring safety. To realize these concepts of "high accuracy," "miniaturization/light weight," and "redundancy," electronic components must deal with problems of increasing loss (heat generation, power consumption), insufficient heat resistance, etc.
Circuit Configuration of ESC
Overall configuration
- Transceiver:A device or circuit that communicates with external equipment (through CAN).
- Microcomputer (MCU):Processes/evaluates data, and controls the motor and brake pressure valve.
- DC/DC converter:Supplies power to the MCU and transceiver.
- Motor drive circuit:A power supply for driving the motor.
- Valve drive circuit:A power supply for driving the brake pressure valve.
- Motor:Controls the pressure of the whole hydraulic system.
- Valve:Controls the pressure adjustment valve of each brake.
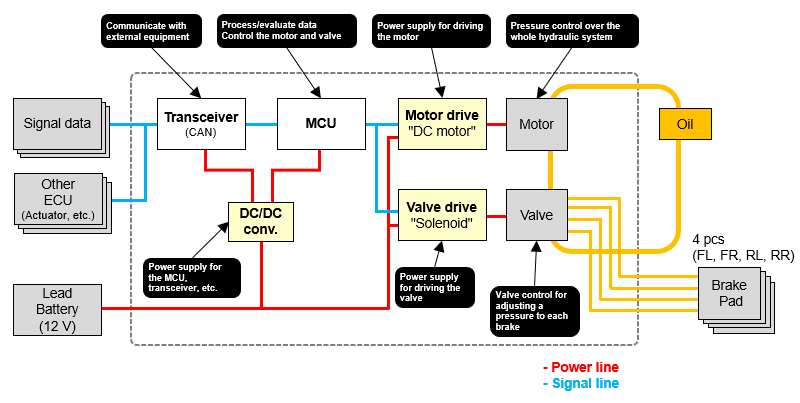
Individual Circuits and Components
Transceiver
The transceiver (circuit) communicates with external equipment through two communication lines (CAN, Ethernet, etc.). If noise or static electricity enters these communication lines, it may cause a transceiver IC to fail. To prevent such a problem, the transceiver IC is usually provided with chip varistors serving as electrostatic control measures.
ESD noise elimination: Chip varistor
POINT- ❶ With a wide range of capacitance characteristics, the chip varistor suppresses electrostatic discharge (ESD) noise while keeping the communication quality of the circuit intact.
- ❷ With its capacitance ranging from 8 pF to 250 pF, the chip varistor operates effectively at low and high communication speeds.
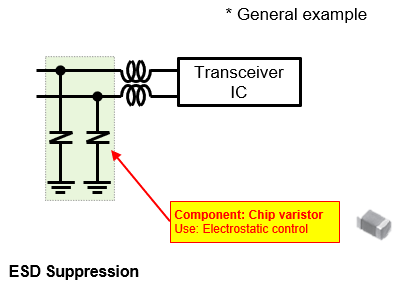
DC/DC converter
The DC/DC converter is composed mainly of an FET, a coil, and capacitors. In the DC/DC converter, generally, conductive polymer hybrid aluminum electrolytic capacitors are used to eliminate noise at the input end and to smooth voltage output at the output end, an in-vehicle power inductor is used for voltage conversion, and a chip resistor (high-precision chip resistor) is used for voltage measurement.
Noise elimination, switching, and smoothing: Conductive polymer hybrid aluminum electrolytic capacitor
POINT- ❶ The capacitor offers high capacitance, low ESR, and high ripple-suppression performance, thus contributing to a reduction in the size of the circuit and an increase in the power capacity (low voltage and large current) of the circuit.
- ❷ Having capacitance characteristics that can cut off high-frequency components, the capacitor eliminates a wide range of high-frequency noises that are generated by a high-frequency switching of the circuit.
Voltage conversion: Power Inductors for Automotive application
POINT- ❶ Inductors made of a metallic magnetic material suffer less power loss and carry a large current, thus contributing to a reduction in the size of the circuit and an increase in the power capacity (low voltage and large current) of the circuit.
- ❷ Having loss characteristics in a higher frequency range (low ACR), the inductor contributes to the suppression of power loss caused by high-frequency switching of the circuit.
Voltage measurement: Chip resistor (high-precision chip resistor)
POINT- ❶ The chip resistor with a thin-film structure offers a small resistance tolerance and a low TCR, thus contributing to high-precision control of the output characteristics of the circuit.
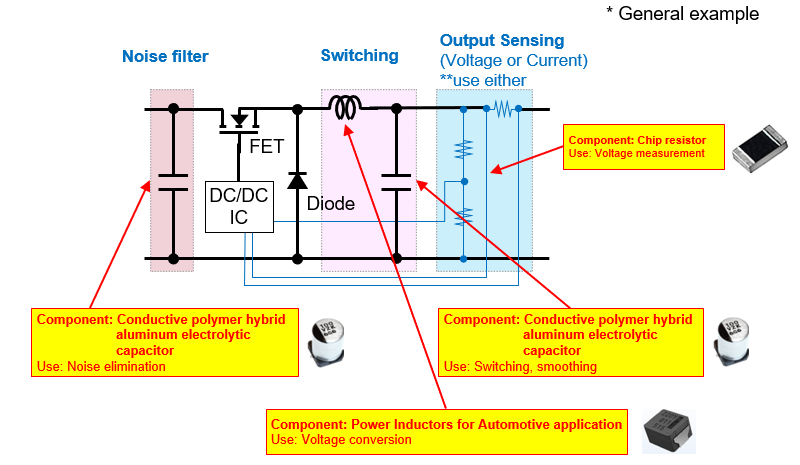
Motor drive circuit
The motor drive circuit converts voltage by switching elements. The switching elements’ switching actions cause input voltage to fluctuate, thus creating noise. To filter out this noise, a noise filter composed of a coil and a capacitor is provided. The switching elements switch on and off to make voltage conversion, but these switching actions create noise. To suppress this noise, resistors at the gate terminals of these switching elements are provided.
Noise elimination and smoothing: Conductive polymer hybrid aluminum electrolytic capacitor
POINT- ❶ The capacitor offers high capacitance, low ESR, and high ripple-suppression performance, thus contributing to a reduction in the size of the circuit and an increase in the power capacity (low voltage and large current) of the circuit.
- ❷ Having capacitance characteristics that can cut off high-frequency components, the capacitor eliminates a wide range of high-frequency noises that are generated by a high-frequency switching of the circuit.
Noise elimination and smoothing: Power Inductors for Automotive application
POINT- ❶ Inductors made of a metallic magnetic material suffer less power loss and carry a large current, thus contributing to a reduction in the size of the circuit and an increase in the power capacity (low voltage and large current) of the circuit.
- ❷ Having loss characteristics in a higher frequency range (low ACR), the inductor contributes to the suppression of power loss caused by high-frequency switching of the circuit.
Suppressing gate-driven noise from the switching elements: Chip resistor (small and high-power chip resistor)
POINT- ❶ With its original resistance pattern, electrode structure, etc., the chip resistor is small in size and yet handles high-power operations, thus contributing to a reduction in the size of the circuit.
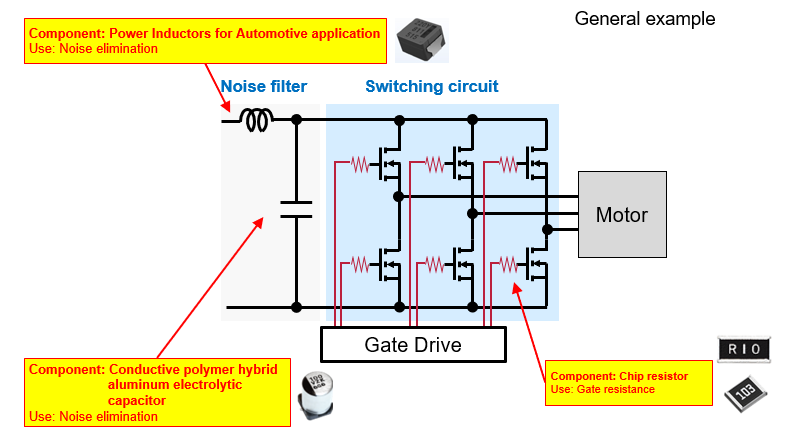
Valve drive circuit
The valve drive circuit causes a solenoid to switch on and off, thereby actuating the valve. The valve drive circuit is composed of the solenoid, a diode for protection against surge, and an FET for on/off control. Because the FET’s switching on and off creates noise, its gate terminal is provided with a resistor that suppresses the noise.
Suppressing gate-driven noise from the switching elements: Chip resistor (small and high-power chip resistor)
POINT- ❶ With its original resistance pattern, electrode structure, etc., the chip resistor is small in size and yet handles high-power operations, thus contributing to a reduction in the size of the circuit.
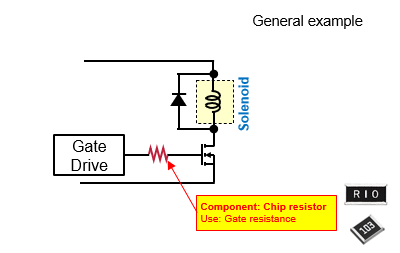
Summary
ESC is vehicle safety technology that combines together ABS, TCS, and yaw control. This technology stabilizes the vehicle position, prevents skidding of the vehicle, and assists the driver in performing proper braking operation. Currently, many vehicles are equipped with ABS or ESC, and vehicles carrying these systems are expected to increase in future. Equipment included in these systems needs to achieve high accuracy in brake control and to meet a demand for miniaturization and redundancy at a system level. In addition, electronic components making up such equipment must meet requirements for less loss and improved heat resistance. Panasonic Industry offers a wide variety of products for use in ESC (Table 1).
Component | Feature | Low loss |
Small size |
High resistance to heat |
---|---|---|---|---|
![]() |
Low ESR High reliability |
✔ | ✔ | ✔ |
Power Inductors for Automotive application ![]() |
Large current, low loss High reliability |
✔ | ✔ | ✔ |
![]() |
High precision, high resistance to heat | ✔ | ✔ | |
Chip varistor![]() |
Small and light | ✔ |
Related product information
Related information
Tags related to this article
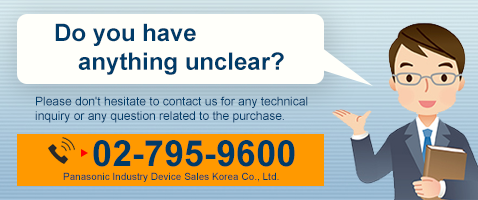