In-Line Process: The process head can be installed in NPM line by means of plug and play
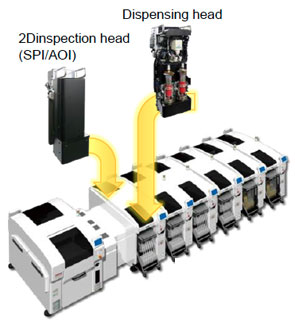
Dispensing head
- Adhesive dispensing for reinforcing the joints of major components
- Corner adhesive method (Drawing function)
- Solder dispensing
2D inspection head
- Solder printing inspection
(misalignment, Oozing, blur) - Pre-reflow AOI
(misalignment, missing, IC polarity) - Shield case pre-placement inspection
M2M (Equipment between the communication control)
Good production APC system
Feedback control(APC-FB)
Printing position correction values (X, Y, θ) statistically processed from the SPI printing position measurement results are sent M2M(FB) to improve printing quality (prints in the “correct position")
Feedforward control (APC-FF)
Mounting position correction values (X, Y, θ) based on measured solder printing position are sent M2M(FF) (target the solder position and mount) to improve post-reflow quality
Automatically corrects variations on the machine side to inhibit the occurrence of defects
Feedback control(APC-MFB)
Inline calibration
Mounting position correction values (X, Y, θ) statistically processed from the AOI mounting position measurement results are sent M2M(FB) to maintain and improve the accuracy of the mounting position and improve quality post-reflow (mount in the targeted position as intended)
Panasonic APC system enables M2M with other company’s SPI / AOI
Panasonic forms an alliance with other companies’ inspection device makers in order to utilize the APC system for better production based on their SPI/AOI inspection information.
*Only certain makers can support APC-MFB from AOI. Please ask us.
Alliance of inspection device makers
Nagoya Electric Works | Koh-Young |
TRI | Cyber Optics |
PARUMI | Viscom |
CKD | MIRTEC |
Inspection device information display
(Evolved M2M function)
In case AOI judges any defect, information of the placement machine used for mounting is displayed on the AOI screen [1].
In addition, if AOI judges that modification of the machine is required, AOI sends warning to the applicable machine via machine communication. The inspection result and AOI image are displayed on the operation screen of the applicable machine so that the nozzle/feeder used for mounting can be directly identified [2].
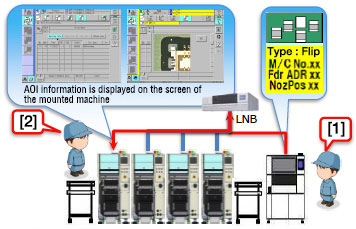
Automated/labor saving function enhancing autonomous mounting line
There are many factors that cause to stop the machine in the mounting line, resulting in variation in throughput and quality. The Panasonic automated/labor saving function achieves labor saving in the mounting line using “Automatic recovery", “Remote operation" and “Navigation" and controls manufacturing variability.
Cases of machine stop and Operator’s work
|
Panasonic automated/labor saving solutions |
|||||||||||||||||
![]() |
|
|||||||||||||||||
![]() |
|
|||||||||||||||||
![]() |
|
Automatic recovery of pickup/recognition error
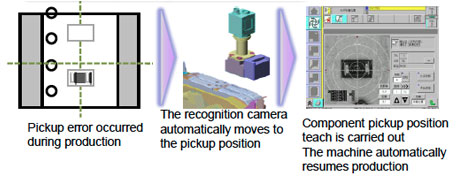
When the machine detects a pickup error or recognition error, it automatically performs operations (pickup position teach) required for machine restart. Therefore, a line operator does not need to do recovery operation. Because the function can reduce the number of events that several placement machines stop at the same time, it is very effective for labor saving.
Navi of Parts supply
A component supply support tool that navigates efficient component supply priorities.
It considers the time left until component run-out and efficient path of operator movement to send component supply instructions to each operator. This achieves more efficient component supply with to suppress the generation of component supply waiting stop.
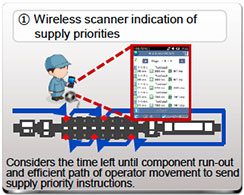
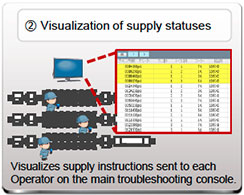
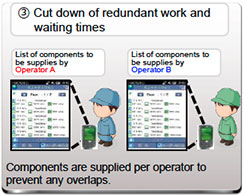
*PanaCIM-EE is required if an operator is in charge of supplying components to multiple production lines.
Automation items
Automates operations that were dependent with operator/engineer experience or skill.
They can offer stable productivity/quality to reduce production variation resulting from difference in operator skill.
Automatic tape splicing unit,
ATSU
Automates splicing operation of 8mm width tape (paper/embossed) with non-technical skills.
Constant splicing man-hour.
Power cordless anywhere to use (Lead-acid battery drive)
Feeder maintenance unit,
IFMU
Automates the inspection of major parts which affect the feeder performance and the calibration of the pickup position.
Prevents the outflow of defective feeders to the site while maintaining high mounting quality.
Head maintenance unit
Automates placement head maintenance with non-technical skills.
Maintains mounting quality due to performing maintenance and inspection at the same time together with inspection.
Constant maintenance man-hour.